KeithB
Resident Half Fast Machinist
Cleaning up shop, going through years of accumulated junk, finding all sorts of things.
When I first became I machinist I ran a machine called a planer, specifically a Gray double column four head machine with a 72" wide table and a twenty foot long stroke. We would take rough castings for the mainframes of Bucyrus-Erie cranes and shovels and plane flat surfaces where necessary. The first part I ran weighed about 15 tons, and when we rough cut using all four heads we would cut off several hundred pounds of chips per hour.
Here are photos of one of the chips that I cut off and managed to take home. It was a cut taken in medium alloy medium carbon steel using a large (fist size) Apex HSS tool cutting 1" deep with a 1/4" feedrate per stroke. Cutting velocity was probably 25 or so feet/min.
Remember, the machine was cutting FOUR of these at a time...
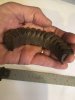
When I first became I machinist I ran a machine called a planer, specifically a Gray double column four head machine with a 72" wide table and a twenty foot long stroke. We would take rough castings for the mainframes of Bucyrus-Erie cranes and shovels and plane flat surfaces where necessary. The first part I ran weighed about 15 tons, and when we rough cut using all four heads we would cut off several hundred pounds of chips per hour.
Here are photos of one of the chips that I cut off and managed to take home. It was a cut taken in medium alloy medium carbon steel using a large (fist size) Apex HSS tool cutting 1" deep with a 1/4" feedrate per stroke. Cutting velocity was probably 25 or so feet/min.
Remember, the machine was cutting FOUR of these at a time...
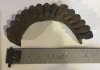
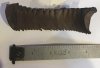
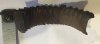
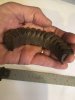