An Alternate Annealing Methodology
Ric Bowman (RicinYakima)
Something as simple as annealing brass should not be as expensive or time consuming as it always seems to be in the doing. The following is not my invention, but that of Mike Rector, a noted metallurgist and engineer who also shoots Creedmoor Style BPCR. You only need three things: a PID lead pot controller, an aluminum plate that will float on the top of the lead pot and an aluminum cooling plate.
I have a small four pound Lee pot that is just about perfect. When almost full, I float a round plate of aluminum into which I have drilled a center hole for the PID probe to go to the bottom of the pot, and 12 blind holes for the case necks to fit into. I was only concerned with 30/06 case necks, so I used an 11/32” drill, but it requires sized cases or they stick when they get hot. The next time I get the drill press out I will open then up with the “S” size drill bit. It requires a temperature of 658 F. for one hour to anneal brass, but at 750 F. it only requires 30 seconds. The PID is set for 750 F.
The operation is simple: put 10 cases neck down in the holes one at a time, then with needle nose pliers, take the first in case out and set it head down in the aluminum block until you have all ten cooling. Put ten more into the floating plate, then remove them and put them into the cooling block. The first ten are cool enough to put back into the plastic boxes with bare fingers! But now the floating plate is back to temperature, so put in ten more cases, then put those to cool in the block. The second ten are ready to box up. It took me 20 minutes to do the first 100 cases, but in the next 30 minutes I did 300 more cases. There is a natural safety factor with cases over two inches in length. Regardless of the time I left an un-primed case heat, it would not get hotter than 650 F over one inch above the plate. I carefully checked with a heat stick crayon and 30/06 and longer cases loose heat so fast, it can anneal no higher than that at a setting of 750 F.
Some warnings: I tried to do 7.62 X 39 cases, but they have so little mass and are so short that it annealed almost up to the extractor cut in 30 seconds. 30/30 Winchester cases were done in 10 seconds, so you have to different timing and / or temperature values. The floating plate’s holes shrink as it heats, the first un-sized case I tried stuck and I had to take everything apart and cool it to get it out. There has to be enough lead in the pot for the plate to have full bottom contact, or you will not have the same heat on all cases.
April 10, 2014
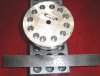
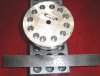
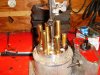
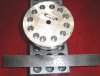
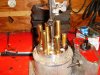