Ian
Notorious member
Bought this once-nice Ideal 357446 single-cavity off of a SS board years ago, it was kind of an orphan and priced right. Unfortunately, the person I bought it from decided to knock the faint surface rust inside the cavities with a WIRE WHEEL. Jeezless people. When it arrived there was a big ridge of metal piled up on one side of each cavity edge. I tried to peen the metal back into place, but one side was too trashed. See the bullet cast from the mould down at the bottom.
I wanted to try a heavy .45 Colt bullet design that's been running through my head lately so I figured why not try to fix this one. I had one more piece of 3/16 tool steel from KeithB's grab box so I ground a profile tool and.........(hours of fiddling and nail biting) I got just what I wanted, almost. 300 grains/.454" was the goal an it ended up 310/.455. I undershot the diameter the first time and had .003" taper toward the front so back in the lathe it went. I also wanted the bands a bit wider so I plunged the cutter some. It was perfect except I forgot to pull the cutter back to zero to clean up the undersized portions left from enlarging/straightening the cavity, so back in the lathe for a third time, and this time I had to get it indicated perfectly on axis because I was out of lee-way to clean it up again. Finally I got it where I wanted it but ended up over-shooting a thousandth. That's ok, it cleans up fine in the sizer.
The final test batch I cast in a hurry and didn't get the bands really sharp, but that's no reflection on the cut of the mould, it turned out nice and I'm really happy that this fine old tool can work again.
By the way, this is an absolutely screwball way to cut a mould due to the incredibly high tool load and I'm not sure it would be realistic to do multiple cavities. I can only imagine that Tom and others who lathe-cut their moulds use a cnc setup and a single point tool to make multiple passes.
I wanted to try a heavy .45 Colt bullet design that's been running through my head lately so I figured why not try to fix this one. I had one more piece of 3/16 tool steel from KeithB's grab box so I ground a profile tool and.........(hours of fiddling and nail biting) I got just what I wanted, almost. 300 grains/.454" was the goal an it ended up 310/.455. I undershot the diameter the first time and had .003" taper toward the front so back in the lathe it went. I also wanted the bands a bit wider so I plunged the cutter some. It was perfect except I forgot to pull the cutter back to zero to clean up the undersized portions left from enlarging/straightening the cavity, so back in the lathe for a third time, and this time I had to get it indicated perfectly on axis because I was out of lee-way to clean it up again. Finally I got it where I wanted it but ended up over-shooting a thousandth. That's ok, it cleans up fine in the sizer.
The final test batch I cast in a hurry and didn't get the bands really sharp, but that's no reflection on the cut of the mould, it turned out nice and I'm really happy that this fine old tool can work again.
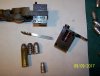
By the way, this is an absolutely screwball way to cut a mould due to the incredibly high tool load and I'm not sure it would be realistic to do multiple cavities. I can only imagine that Tom and others who lathe-cut their moulds use a cnc setup and a single point tool to make multiple passes.