Lee bullet moulds may be the most controversial moulds available to the bullet caster today ?
They are praised by many and cursed by the rest.
My goal in this thread is not to promote or malign Lee bullet moulds.
You may already have a strong opinion on the subject and most likely I won't be able to sway you one way or the other.
However, if you do decide to invest $20 in one of these moulds there are a few things that you should know and do if you hope to get any service at all out of the mould.
For a long time, I've been a fan of the Lyman/IDEAL 358156 . Skeeter Skelton said it was his all time favorite in his Model 19 Smith that he carried for duty use. He shot the bullet with 13.5 grs. of 2400 seated out long in the 38 Spec. case. In my opinion, that load is more than a " bit stiff ". If I were shooting that load today, I'd be certain it was in a 357 Mag. gun and I'd drop back to 11.5 grs. of 2400.
I ordered this mold a few days ago on a " whim ". I already own 3 Lyman / Ideal 358156 molds , one is a solid, the other two are HP molds. GREAT MOLDS ! !
This particular Lee mold has always reminded me of the IDEAL 358156 design.
I thought it might be worth a try ? ?
Once the mold arrived, I began the " Lee Menting process ".
The gas check " clicks and snaps " on with a nice tight fit.
Both cavities on my particular mould drop at 160 grs. with 50% range scrap and 50% WW's and are within .0003 " of being perfectly round. There was no sticking of the bullets in the mould cavities. A gentle tap on the hinge bolt and both cast bullets fell freely from the mould.
The lube capacity on the Lee mould is greater than the lube capacity of the IDEAL 358156 mould. If you're shooting this bullet out of a long barrel .357 rifle, this additional lube feature may benefit you ?
They are praised by many and cursed by the rest.
My goal in this thread is not to promote or malign Lee bullet moulds.
You may already have a strong opinion on the subject and most likely I won't be able to sway you one way or the other.
However, if you do decide to invest $20 in one of these moulds there are a few things that you should know and do if you hope to get any service at all out of the mould.
For a long time, I've been a fan of the Lyman/IDEAL 358156 . Skeeter Skelton said it was his all time favorite in his Model 19 Smith that he carried for duty use. He shot the bullet with 13.5 grs. of 2400 seated out long in the 38 Spec. case. In my opinion, that load is more than a " bit stiff ". If I were shooting that load today, I'd be certain it was in a 357 Mag. gun and I'd drop back to 11.5 grs. of 2400.
I ordered this mold a few days ago on a " whim ". I already own 3 Lyman / Ideal 358156 molds , one is a solid, the other two are HP molds. GREAT MOLDS ! !
This particular Lee mold has always reminded me of the IDEAL 358156 design.
I thought it might be worth a try ? ?
Once the mold arrived, I began the " Lee Menting process ".
- The sprue place must be removed and the edges " rolled " to remove the saw tooth edges that Lee seems to always have on their sprue plates.
- To remove the sprue plate on the " new style Lee Molds ", be aware that the sprue bolt that holds the sprue plate in place has left hand threads on it.
- The plate is on so tight from the factory, you're guaranteed to damage the mold in the first 10 minutes of use without this work described here.
- I drill and tap a 10-24 hole for a sprue bolt lock screw. ( see photos below )
- The mold is cleaned well with hot soapy water and a soft tooth brush.
- Everything is dried with compressed air and a propane torch.
- I then lubed the tops of the blocks and the underside of the sprue plate with a TINY dab of 2 cycle oil. Then both surfaces are rubbed with a soft cotton cloth to remove any excess 2 cycle lube.
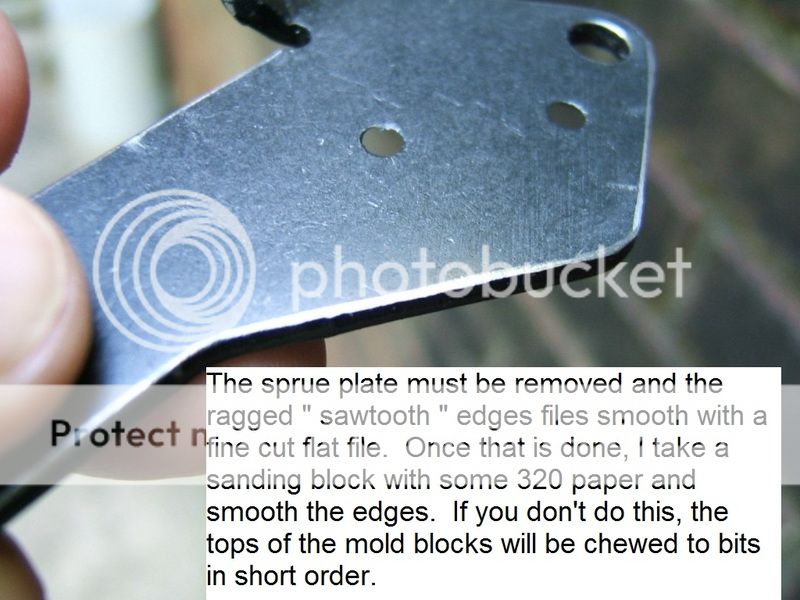
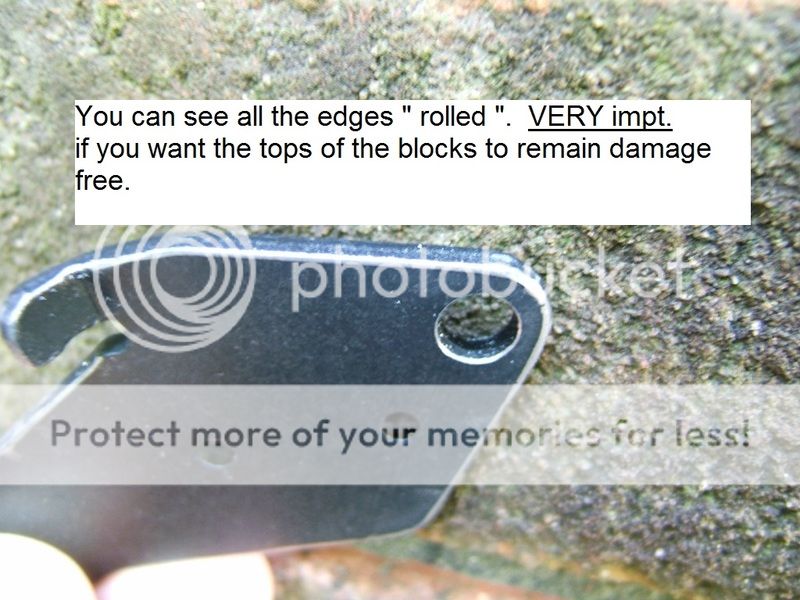
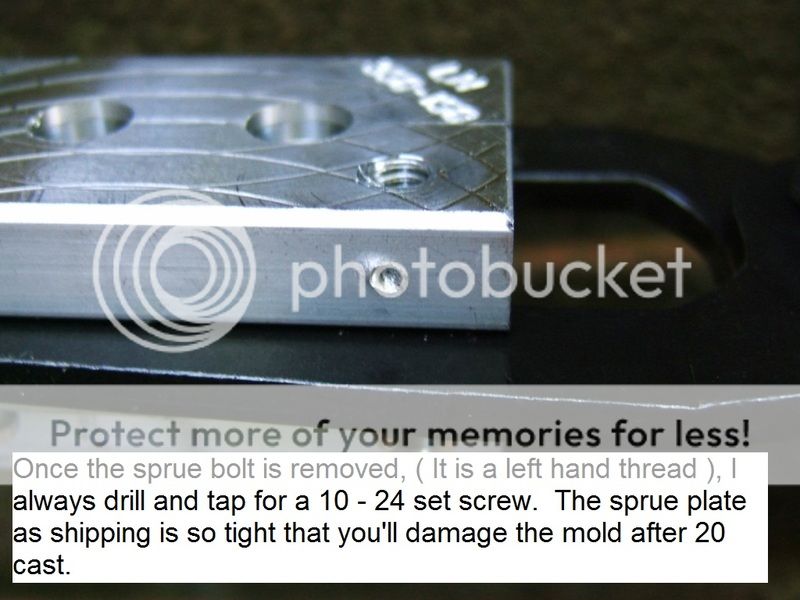

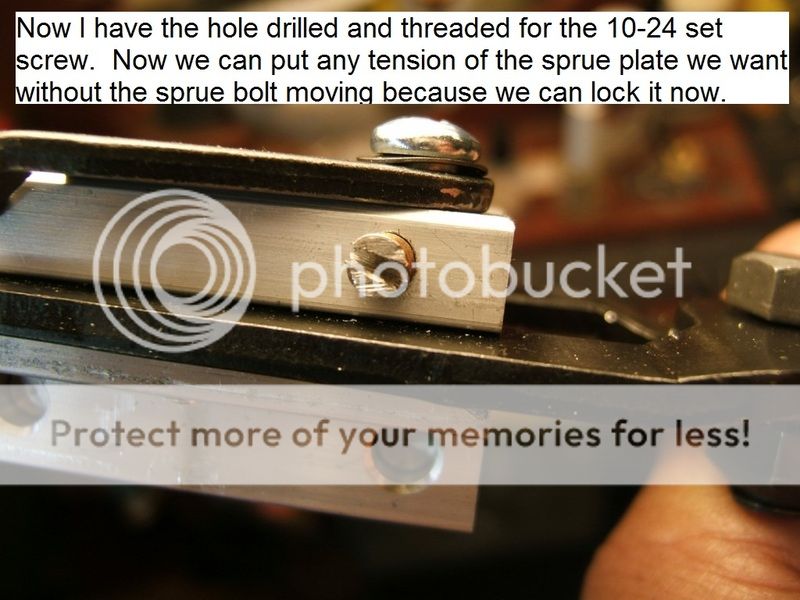
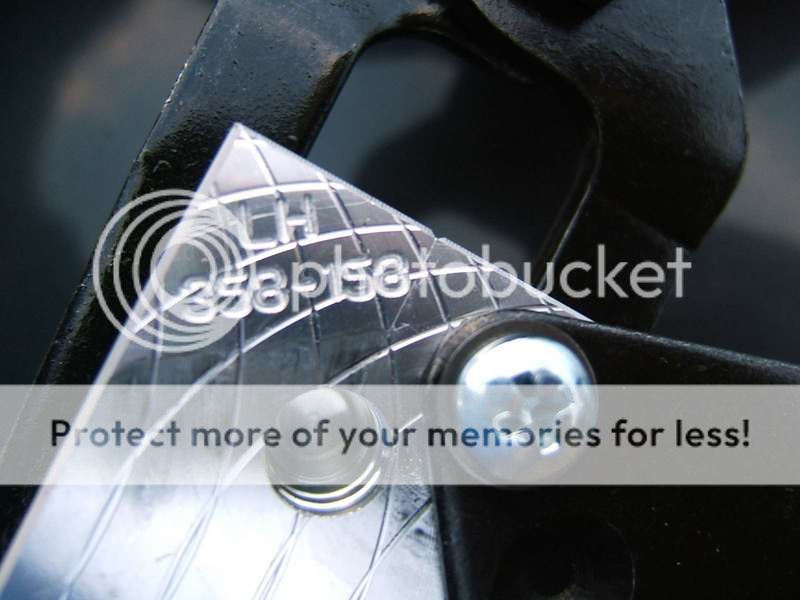
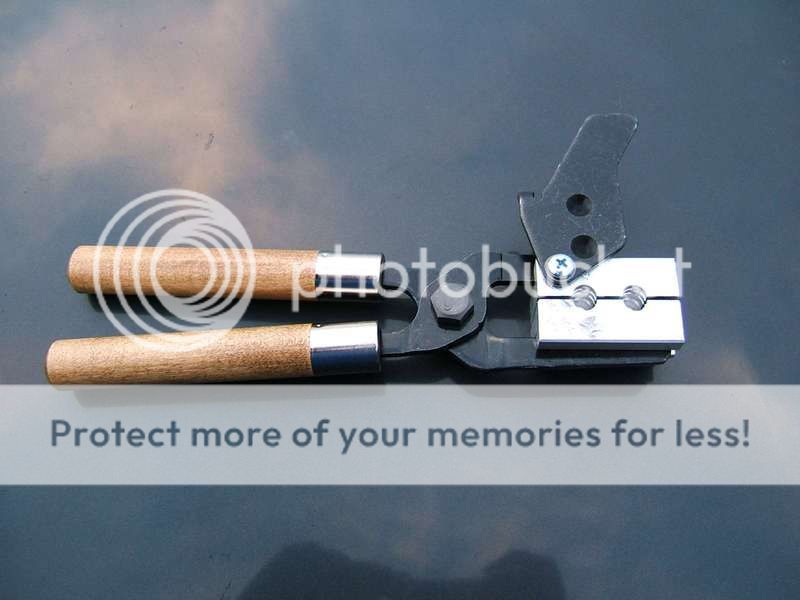
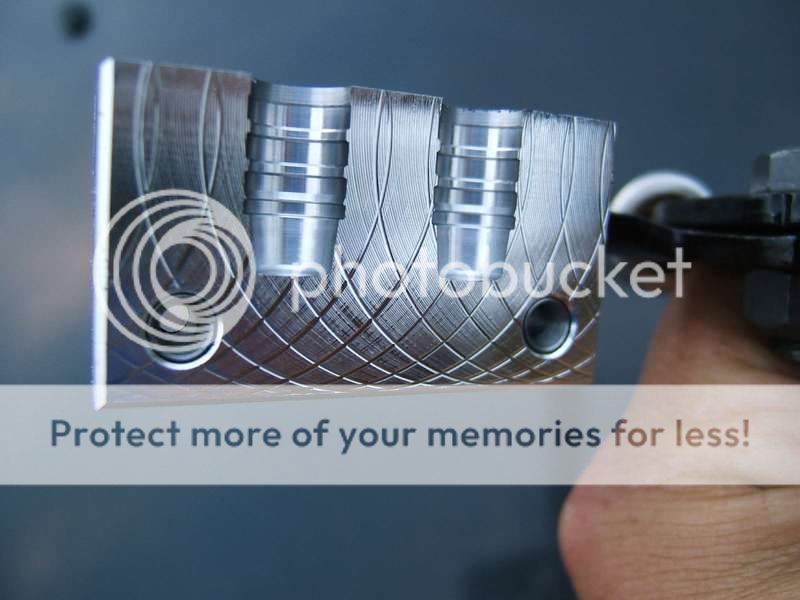
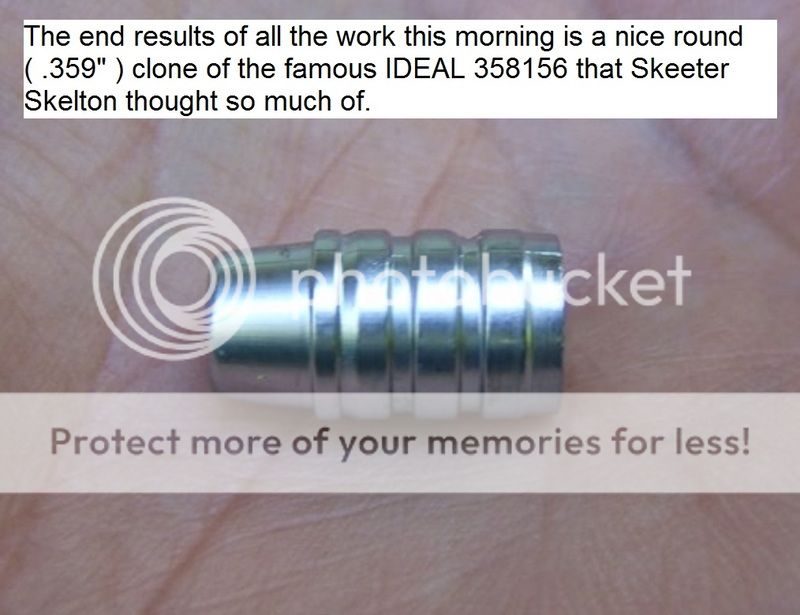
The gas check " clicks and snaps " on with a nice tight fit.
Both cavities on my particular mould drop at 160 grs. with 50% range scrap and 50% WW's and are within .0003 " of being perfectly round. There was no sticking of the bullets in the mould cavities. A gentle tap on the hinge bolt and both cast bullets fell freely from the mould.
The lube capacity on the Lee mould is greater than the lube capacity of the IDEAL 358156 mould. If you're shooting this bullet out of a long barrel .357 rifle, this additional lube feature may benefit you ?
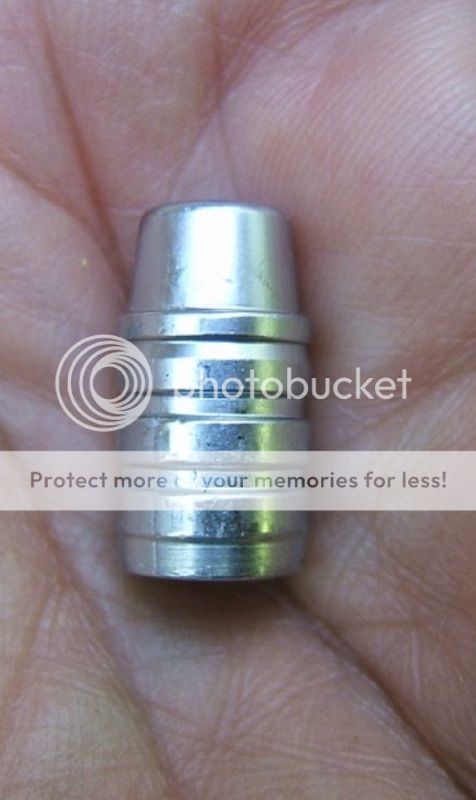
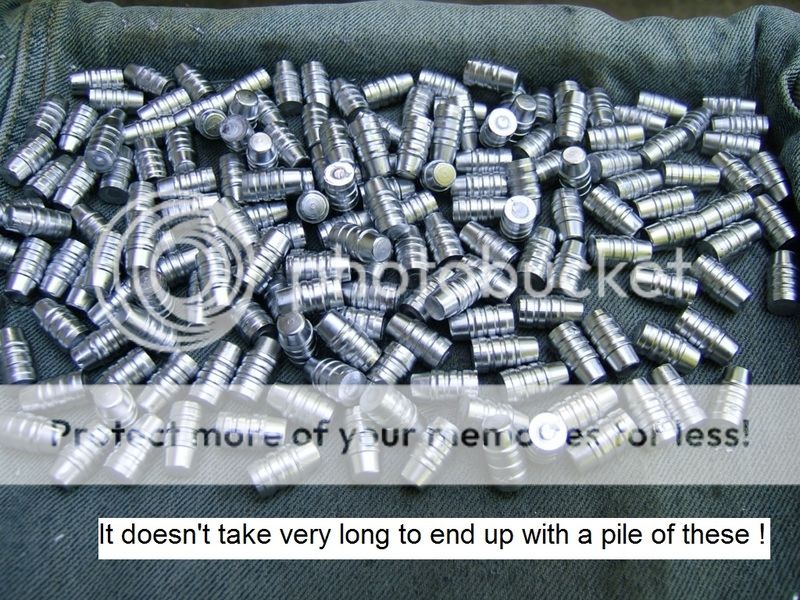
Last edited: