Waco mentioned in a different thread that he was having issues with the Marlin jam.
The problem starts with the cam right in front of the hole for the lever screw. Notice how the cam on this lever has a slight radius? That is good. If it has a sharp corner it tends to cut a groove I to the bottom of the carrier. That lets the carrier drop too low and it doesn't cut off the magazine properly. A second round tries to feed and since it is 1/2 in the action and 1/2 in the tube it binds the carrier. Carrier can't rise so the lever is jammed in the open position. Either remove the lever and take out the offending round or use a small dowel to shove the offending round into the magazine enough to let the carrier rise.
This is the bottom of the carrier where the damage is done. At the rear end of the flat shown is where the groove starts. No groove here because of the radius on the cam.
Solutions is to add metal back to the carrier. My 32-20 has a small section of razor saw blade on the bottom. I soft soldered it in place as it merely acts as a surface for the cam to slide on. Some people use a small weld to add metal then file it back down. Make sure to cut the radius on the cam or it will come back in time!
I can assure you that a 2 shot lever action sucks. So does a rifle that jams every few magazines full. Makes a guy leave a fine shooting rifle at home a lot. Fix it and the fun returns.
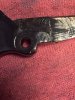
The problem starts with the cam right in front of the hole for the lever screw. Notice how the cam on this lever has a slight radius? That is good. If it has a sharp corner it tends to cut a groove I to the bottom of the carrier. That lets the carrier drop too low and it doesn't cut off the magazine properly. A second round tries to feed and since it is 1/2 in the action and 1/2 in the tube it binds the carrier. Carrier can't rise so the lever is jammed in the open position. Either remove the lever and take out the offending round or use a small dowel to shove the offending round into the magazine enough to let the carrier rise.
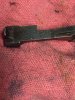
This is the bottom of the carrier where the damage is done. At the rear end of the flat shown is where the groove starts. No groove here because of the radius on the cam.
Solutions is to add metal back to the carrier. My 32-20 has a small section of razor saw blade on the bottom. I soft soldered it in place as it merely acts as a surface for the cam to slide on. Some people use a small weld to add metal then file it back down. Make sure to cut the radius on the cam or it will come back in time!
I can assure you that a 2 shot lever action sucks. So does a rifle that jams every few magazines full. Makes a guy leave a fine shooting rifle at home a lot. Fix it and the fun returns.
Last edited: