KeithB
Resident Half Fast Machinist
One of the more common machinist's problem is threading up to a shoulder. The solution is to cut away, not towards a shoulder. When cutting standard RH threads the lathe spindle is turning CCW (viewed from them front) and the tool travels from the right side to the left, It requires a lot of eye-hand coordination to stop the lathe at the right place so as not to run into a shoulder. It is a lot less demanding to run the spindle in reverse (CW) and have the tool travel from the left side to the right. The problem is orienting the cutting edge of the tool in the right position, by (a) mounting the tool with the cutting face up in a position on the back side of the part, or (b) mounting the tool upside down on the near side of the part.
On my manual lathe there is no practical way to mount a tool on the far side of the part, (I can and often do that on the CNC lathe) That meant I needed to figure out a way to mount a threading tool upside down in my Aloris tool holder.
My solution was to make a rectangular block 3/4" x 1-1/2" x 3-1/2" from a piece of steel scrap. I drilled and tapped two 1/4-20 holes in it. Then I took one of our spare laydown type threading tool holders and drilled two 17/64" holes to match. Bolt the tool holder upside down to the block and clamp the block in the slot of an Aloris type tool holder and its ready to cut.
I didn't have time to try this setup but I know the carbide laydown inserts are capable of cutting beautiful threads so I don't expect any problems. The toolholder I used is a RH version and as can be seen it means that the cutting point is 3/4" from the left, It would be hard to cut up to a shoulder on the left so I ordered another toolholder only in a LH version. I will also have to buy left hand inserts but that's no problem
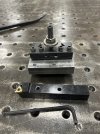
.
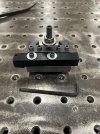
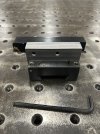
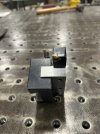
On my manual lathe there is no practical way to mount a tool on the far side of the part, (I can and often do that on the CNC lathe) That meant I needed to figure out a way to mount a threading tool upside down in my Aloris tool holder.
My solution was to make a rectangular block 3/4" x 1-1/2" x 3-1/2" from a piece of steel scrap. I drilled and tapped two 1/4-20 holes in it. Then I took one of our spare laydown type threading tool holders and drilled two 17/64" holes to match. Bolt the tool holder upside down to the block and clamp the block in the slot of an Aloris type tool holder and its ready to cut.
I didn't have time to try this setup but I know the carbide laydown inserts are capable of cutting beautiful threads so I don't expect any problems. The toolholder I used is a RH version and as can be seen it means that the cutting point is 3/4" from the left, It would be hard to cut up to a shoulder on the left so I ordered another toolholder only in a LH version. I will also have to buy left hand inserts but that's no problem
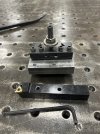
.
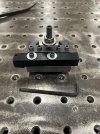
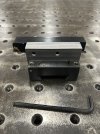
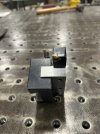