wquiles
Well-Known Member
My best friend and I both have a 5th gen 4Runner (mine the Limited has a sunroof, his SR5 does not) and we wanted a roof rack to aid carrying stuff while camping. We feel the Gobi is the best rack out there, but pricey, and since I can weld, I figured we could do/built our own. I found this DIY article, and decided to create a sort-of-hybrid design with ideas from the article, things we liked about the Gobi, and a couple of 4Runner DIY articles from other folks that have also done a DIY roof rack.
I modified the design from the DIY in several ways by adding extra cross supports, using 14g steel, making the outer frame fully-enclosed/sealed, making the rack full length, including designing a wind deflector, adding side mounting points (1/4" thick), wider load-bearing mount surfaces (more on this later), etc. I was not in a particular hurry so I actually Tig welded everything on both racks:
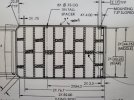
Although my garage floor is far from flat, we used it as a starting point to get the outer frame:
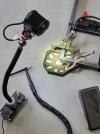
Another design change is that we made the inner struts sit exactly one inch from the top of the frame, which gives a 1" lip to prevent items from potentially sliding over, but also means that longer pieces can fit flat against the outer edges of the frame. I literally used hockey pucks to get the 1" spacing:
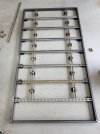
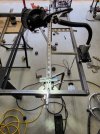
I used my "old" circa-2003 HTP water-cooled Tig welder for everything. Not as modern and lacking options from the more recent HTP 221 model, but it still works well. This is my second HTP welder (my other one is the 2100 MIG welder) and I am super impressed with HTP:
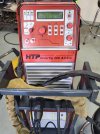
I am still very much learning to weld with Tig, but still did OK for a beginner:
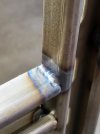
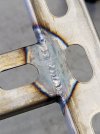
I modified the design from the DIY in several ways by adding extra cross supports, using 14g steel, making the outer frame fully-enclosed/sealed, making the rack full length, including designing a wind deflector, adding side mounting points (1/4" thick), wider load-bearing mount surfaces (more on this later), etc. I was not in a particular hurry so I actually Tig welded everything on both racks:
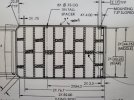
Although my garage floor is far from flat, we used it as a starting point to get the outer frame:
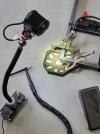
Another design change is that we made the inner struts sit exactly one inch from the top of the frame, which gives a 1" lip to prevent items from potentially sliding over, but also means that longer pieces can fit flat against the outer edges of the frame. I literally used hockey pucks to get the 1" spacing:
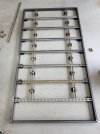
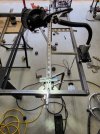
I used my "old" circa-2003 HTP water-cooled Tig welder for everything. Not as modern and lacking options from the more recent HTP 221 model, but it still works well. This is my second HTP welder (my other one is the 2100 MIG welder) and I am super impressed with HTP:
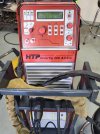
I am still very much learning to weld with Tig, but still did OK for a beginner:
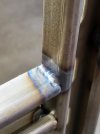
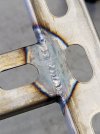
Last edited: