KeithB
Resident Half Fast Machinist
The main reason we bought a big powerful radial arm drill was to offload the work of drilling from our CNC machines whenever possible. One of the products we make is a two-piece pneumatic tailwheel for light aircraft. The blanks are made from 4-1/4" diameter 6061 aluminum. We cut them to 1-1/4" thick. The blanks get a 15/16" hole drilled in the center before they can be run on the CNC lathe. The last time we ran a batch of these (72 pieces) it tied up our CNC lathe for two and a half days. We just got another order for these so I started last Wednesday making a drill fixture.
I finished it up Monday morning. As I was putting the finishing touches on it I managed to get the toe of my prosthetic (left) foot caught under the weld table and I fell rather gracelessly onto the concrete floor, twisting my hip and landing on my right hipbone. Hurt like hell, laid there a few minutes until I was able to get up without help. Managed to make it through rest of day. Got home and took an oxycontin tablet, managed to get to sleep but when I got up in middle of night to go to the bathroom I fell again on my right hip and wife got real concerned. Going to see Dr Thursday afternoon. Going to ask for X-ray to check for cracks in hip socket or head of femur.
Frustrated because I can't test fixture but at least it's finished.
Here is a tailwheel half in mid process. Note the 15/16" center hole.
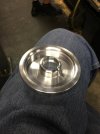
Here is fixture after all the welding and milling has been completed. I'm using a finger indicator to align the fixture in the four jaw chuck.
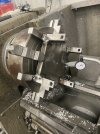
After boring the bottom of the fixture I put the top on and bored it out for the drill bushing.
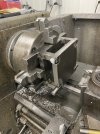
Here is completed fixture in the open position with a test blank.
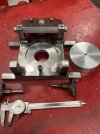
Here is the blank sitting in the fixture.
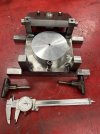
Here is the fixture closed up and ready to use. The two screws sticking out of the top are the clamp screws used to anchor the blank in place

The 3/4" bars on the bottom of the fixture allow for clamping down to the drill's knee table while permitting chips to fall through. I designed the fixture to be easy to use. We should be able to put in the center hole in one pass, no lead drilling required.
I finished it up Monday morning. As I was putting the finishing touches on it I managed to get the toe of my prosthetic (left) foot caught under the weld table and I fell rather gracelessly onto the concrete floor, twisting my hip and landing on my right hipbone. Hurt like hell, laid there a few minutes until I was able to get up without help. Managed to make it through rest of day. Got home and took an oxycontin tablet, managed to get to sleep but when I got up in middle of night to go to the bathroom I fell again on my right hip and wife got real concerned. Going to see Dr Thursday afternoon. Going to ask for X-ray to check for cracks in hip socket or head of femur.
Frustrated because I can't test fixture but at least it's finished.
Here is a tailwheel half in mid process. Note the 15/16" center hole.
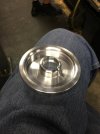
Here is fixture after all the welding and milling has been completed. I'm using a finger indicator to align the fixture in the four jaw chuck.
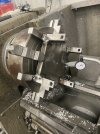
After boring the bottom of the fixture I put the top on and bored it out for the drill bushing.
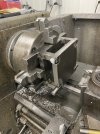
Here is completed fixture in the open position with a test blank.
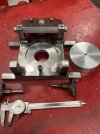
Here is the blank sitting in the fixture.
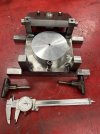
Here is the fixture closed up and ready to use. The two screws sticking out of the top are the clamp screws used to anchor the blank in place

The 3/4" bars on the bottom of the fixture allow for clamping down to the drill's knee table while permitting chips to fall through. I designed the fixture to be easy to use. We should be able to put in the center hole in one pass, no lead drilling required.