JWFilips
Well-Known Member
Hi Guys,
Finally got back into the saddle today! Haven't been able to do much since mid August because of a Sciatica problem that has really set me back but as of a few weeks ago I started to improve each day...so I decided it was time to try casting. Not too bad, but paying a bit now, but the accomplishment was worth it.
Wanted to cast up some Plain Base Noe 165 gr Ranch Dogs for my 30-30 marlin & cast up a bunch of Noe 340-224Gr plain base to be used in my well worn ( now .33 cal ) JP Sauer und Shon 98 Mauser. I size them down to .330 and the shoot great ( thanks to Ben for this idea)!
I also had a run of strange bases...I have seen this before but can't put my finger on it. Not sure if it is because too tight of a sprue plate or too cool of a sprue plate Alloy was run at 720 deg Everything flowing well and a good pool on the plate...only happened on the big 224 grain bullets once in awhile...nothing unusually about the casting session.
Any of you guys know the cause of this ( see 2nd photo)
Thanks
Jim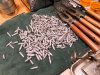
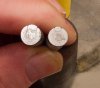
Finally got back into the saddle today! Haven't been able to do much since mid August because of a Sciatica problem that has really set me back but as of a few weeks ago I started to improve each day...so I decided it was time to try casting. Not too bad, but paying a bit now, but the accomplishment was worth it.
Wanted to cast up some Plain Base Noe 165 gr Ranch Dogs for my 30-30 marlin & cast up a bunch of Noe 340-224Gr plain base to be used in my well worn ( now .33 cal ) JP Sauer und Shon 98 Mauser. I size them down to .330 and the shoot great ( thanks to Ben for this idea)!
I also had a run of strange bases...I have seen this before but can't put my finger on it. Not sure if it is because too tight of a sprue plate or too cool of a sprue plate Alloy was run at 720 deg Everything flowing well and a good pool on the plate...only happened on the big 224 grain bullets once in awhile...nothing unusually about the casting session.
Any of you guys know the cause of this ( see 2nd photo)
Thanks
Jim
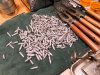
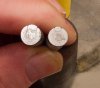