Lookng at the modified M die set up Rick has for flailing checks made me think about making something similar.
I decided to make the entire thing forms scratch, good learning lesson if nothing else.
The body is made from 12L14, threaded to fit press with a 3/8-16 tapped hole in the bottom. The punch is made from annealed O1 as is the anvil the fits the shell holder slot.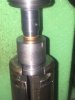
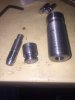
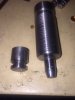
The machining is a bit roug in spots but the nose of the expanding spud is polished well enough that checks come off easily.
Only issue I see is that it is a bit fiddly to get the check centered under the expander. I thought of cutting a small indent the check could sit in but then a new anvil would be required for each size.
What I think would be better is having the expander as part of the shell holder and have the flat anvil be part of the die. Sit a check on the expander, raise the ram to flair, and lower.
I see more time in the garage later today.
I decided to make the entire thing forms scratch, good learning lesson if nothing else.
The body is made from 12L14, threaded to fit press with a 3/8-16 tapped hole in the bottom. The punch is made from annealed O1 as is the anvil the fits the shell holder slot.
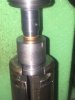
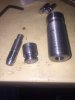
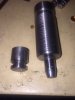
The machining is a bit roug in spots but the nose of the expanding spud is polished well enough that checks come off easily.
Only issue I see is that it is a bit fiddly to get the check centered under the expander. I thought of cutting a small indent the check could sit in but then a new anvil would be required for each size.
What I think would be better is having the expander as part of the shell holder and have the flat anvil be part of the die. Sit a check on the expander, raise the ram to flair, and lower.
I see more time in the garage later today.