Pistolero
Well-Known Member
I picked up a Lyman 55 powder measure a while back for cheap because it had no
outlet funnel/adaptor. Just a big hole in the bottom. Useless as it stands, unless you are
charging shotgun shells, or maybe .577 Nitro Express..barely.
So, I decided to solve another problem with my new toy. Having fun.
I think it turned in nicely.
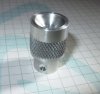
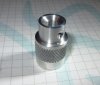
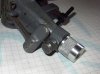
Aluminum sure machines nicely. This will work for .223 up to .45-70, maybe .50-70, haven't
checked yet, made it a bit bigger than the original .495 to the edge of the outlet. I don't load a lot
of .50-70, so not a serious issue.
Bill
outlet funnel/adaptor. Just a big hole in the bottom. Useless as it stands, unless you are
charging shotgun shells, or maybe .577 Nitro Express..barely.
So, I decided to solve another problem with my new toy. Having fun.
I think it turned in nicely.
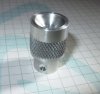
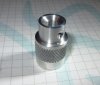
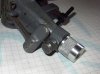
Aluminum sure machines nicely. This will work for .223 up to .45-70, maybe .50-70, haven't
checked yet, made it a bit bigger than the original .495 to the edge of the outlet. I don't load a lot
of .50-70, so not a serious issue.
Bill