Mike W1
Active Member
Anyone know when Lyman changed the shoulder length as well as the OAL of these screws? Without taking a couple more molds aparts to see which have which ones it doesn't make sense to me. I ordered some parts a couple years back and am pretty sure the longer ones are what I got and the invoice description said for .187 cut-off plate. Being a 3/16 plate would be about .1875 and you'd be adding a belleville washer to that, you also need to put another spacer washer in there. With the shorter shoulder that spacer wouldn't be needed. The longer shoulder works fine if I put my thicker aluminum sprue plates in but I've only seen the thinner steel ones on the DC molds I've had. Going to call Lyman tomorrow and order a couple more screws but thought someone on here might know the whys and wherefores.
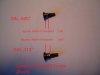
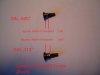
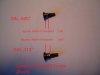
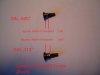