Brother_Love
Well-Known Member
Since I was being lazy this afternoon I thought I would post some pics of my Lee HP conversion. I really like this mold and I graduated to the 6 cavity so I decided to sacrifice the 2c. I ruined the front cavity removing the g/c base so I HP'ed the rear cavity. I used a wood ball from Hobby Lobby, a drill bit for the pin and the collar came from the hardware store. I did this on a woodworking drill press but got lucky and it cast a nice little HP for the 35 Rem and 358 Win.
I would never try this on a steel mold, my tools are not up to that.
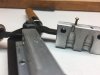
I would never try this on a steel mold, my tools are not up to that.
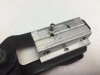
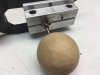
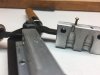