Pistolero
Well-Known Member
Brad's 'Lathey day' post made me think of this project that I just finished.
Working on .38 Spl wadcutter loading for S&W Model 14 and 15 6" target that will produce max
possible accuracy. Starting with Remington swaged HBWCs, since they have a reputation of being
extremely accurate, at least potentially so. Will use my H&G 50 mold to run a comparison
of my own bullets, solid based. Rems are a baseline, and way to learn about HBWCs.
I have some wadcutter brass, and have verified the internal differences with pin gages.
Next I wanted to see if expanding the brass full depth for the bullet would help accuracy, since
the original expander is only about half the length of the bullet and no question that the case
will size down the hollow rear portion to fit the brass, since the alloy is soft and the base is
very deeply hollowed out. Maybe the hollow base blows out to fit the cylinder, even if the
original diam is sized down by the brass - or maybe not. Mr. Target knows the answers.
So - I made a deep expander pin, with the tip at .3580 diam, which pin gages to .357 ID after
expanding WC brass, giving a .001-.002 interference fit on the bullet WITH the thick lube.
Here is a pic of my lathe project, I think it turned out well.
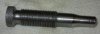
Working on .38 Spl wadcutter loading for S&W Model 14 and 15 6" target that will produce max
possible accuracy. Starting with Remington swaged HBWCs, since they have a reputation of being
extremely accurate, at least potentially so. Will use my H&G 50 mold to run a comparison
of my own bullets, solid based. Rems are a baseline, and way to learn about HBWCs.
I have some wadcutter brass, and have verified the internal differences with pin gages.
Next I wanted to see if expanding the brass full depth for the bullet would help accuracy, since
the original expander is only about half the length of the bullet and no question that the case
will size down the hollow rear portion to fit the brass, since the alloy is soft and the base is
very deeply hollowed out. Maybe the hollow base blows out to fit the cylinder, even if the
original diam is sized down by the brass - or maybe not. Mr. Target knows the answers.
So - I made a deep expander pin, with the tip at .3580 diam, which pin gages to .357 ID after
expanding WC brass, giving a .001-.002 interference fit on the bullet WITH the thick lube.
Here is a pic of my lathe project, I think it turned out well.
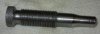