quicksylver
Well-Known Member
Recently I was looking over some pictures I and others have posted on this and other sites.
Quite a few of them were pictures of different bullets side by side..
Some (mine) were of two bullets one NOE and the other Lyman both 299s'.
What I noticed was a striking difference in the location of the lower drive band and consequently
lube grouve...
Then I got to looking at other bullet designs..what caught my eye there was the size of the lube grouve just above the gas check...that's when I started to ask myself... ."why do those designs supply such a large amount of lube to a gas check ?"
My secondary thought was...."would it not be better to have a small lube grouve towards the back / just above the gas check ..with a wide drive band above that and a decent lube grouve (s) above that ?"
Seems to me that would place more weight towards the rear of the bullet and supply lube where it is most needed.....good things right?
Your thoughts...??
Lyman 311 334 Large lube area above gas check
Large and small lube area above gas check
PS... hope this is not out of the topic of "lube"
Quite a few of them were pictures of different bullets side by side..
Some (mine) were of two bullets one NOE and the other Lyman both 299s'.
What I noticed was a striking difference in the location of the lower drive band and consequently
lube grouve...
Then I got to looking at other bullet designs..what caught my eye there was the size of the lube grouve just above the gas check...that's when I started to ask myself... ."why do those designs supply such a large amount of lube to a gas check ?"
My secondary thought was...."would it not be better to have a small lube grouve towards the back / just above the gas check ..with a wide drive band above that and a decent lube grouve (s) above that ?"
Seems to me that would place more weight towards the rear of the bullet and supply lube where it is most needed.....good things right?
Your thoughts...??
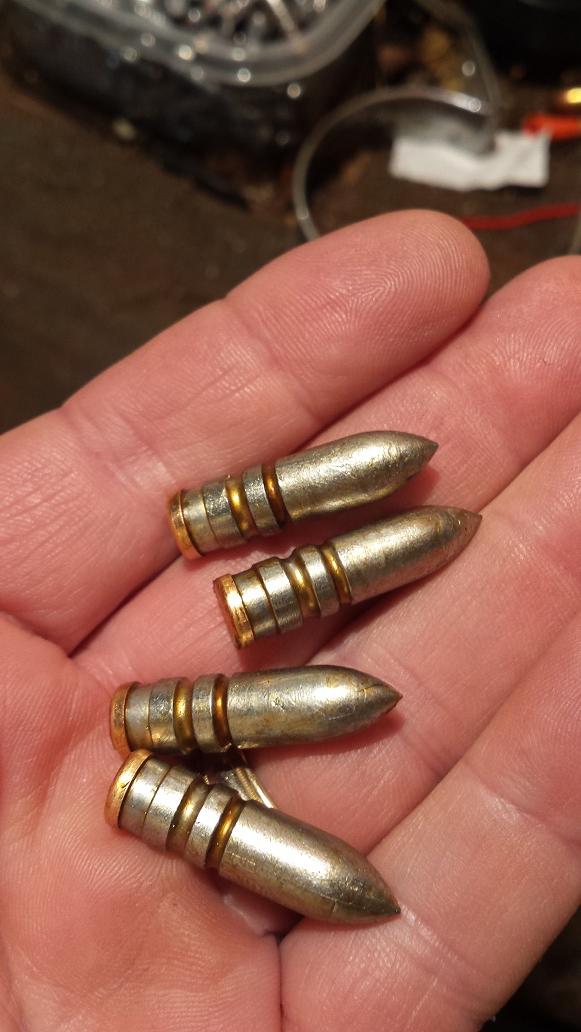
Lyman 311 334 Large lube area above gas check
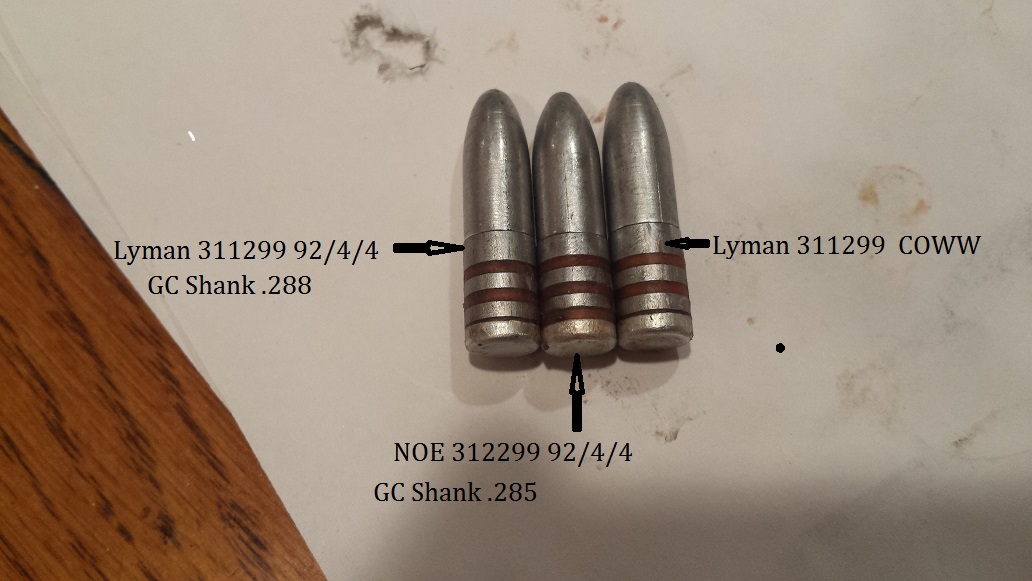
Large and small lube area above gas check
PS... hope this is not out of the topic of "lube"