I have the new mold from MP. Nice tool! .457 257gr, casting in pure lead for a big bore airgun.
I have the mold running hot (350 -400deg) and using a Lyman Mag 25 bottom pour furnace and running a quick cadence to keep the mold nice and hot. Leaving a large sprue puddle and keeping it fluid for a LONG time, but I am consistently getting a shrinkage void above the hollow base core pin (see marked up photo). I even torch heated the pins to try and get this to stop but had not luck. Pressure cast a few and still getting that stinking void, but start getting flash around the base pin, so I know I'm putting the lead to it.
Any ideas? Tricks?
I have the mold running hot (350 -400deg) and using a Lyman Mag 25 bottom pour furnace and running a quick cadence to keep the mold nice and hot. Leaving a large sprue puddle and keeping it fluid for a LONG time, but I am consistently getting a shrinkage void above the hollow base core pin (see marked up photo). I even torch heated the pins to try and get this to stop but had not luck. Pressure cast a few and still getting that stinking void, but start getting flash around the base pin, so I know I'm putting the lead to it.
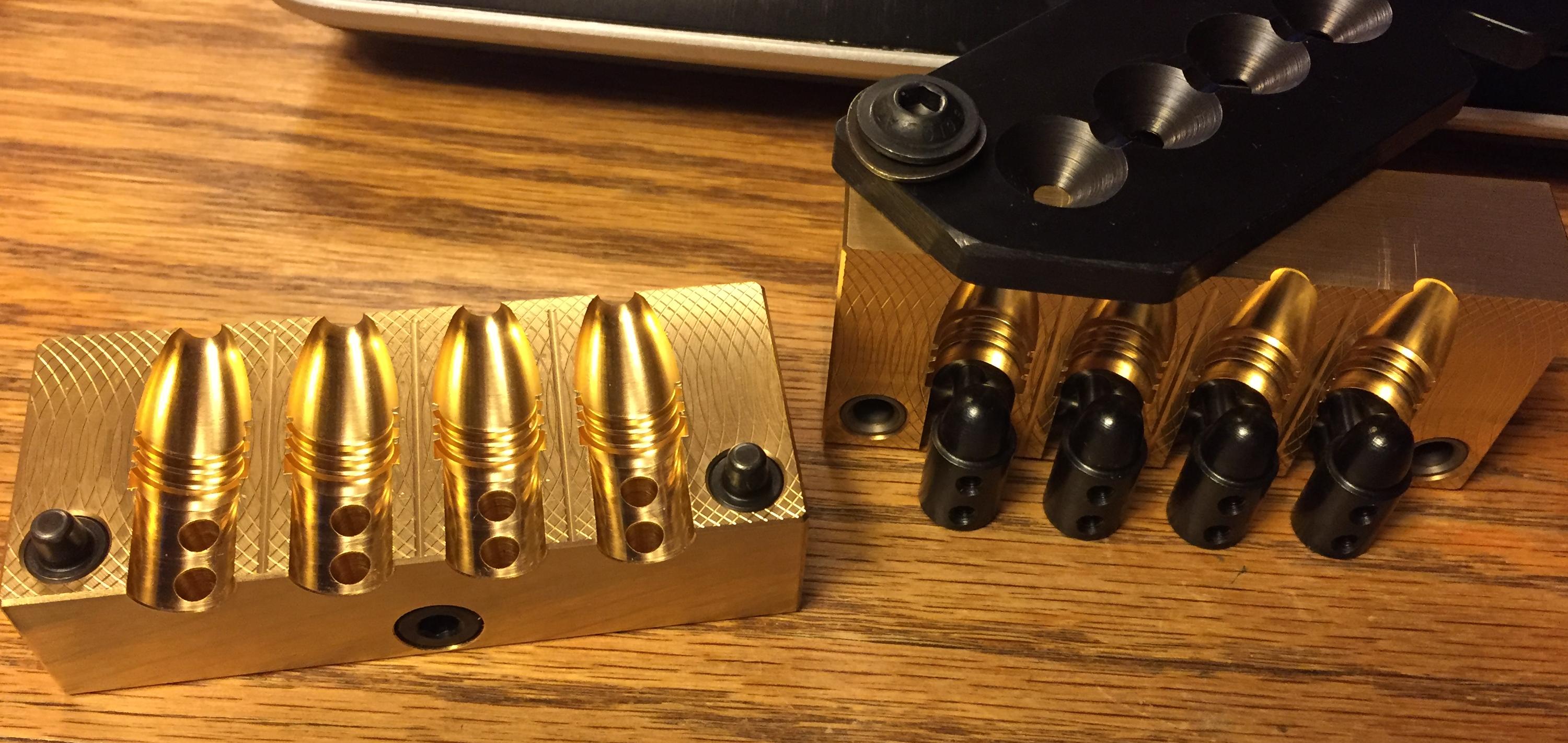
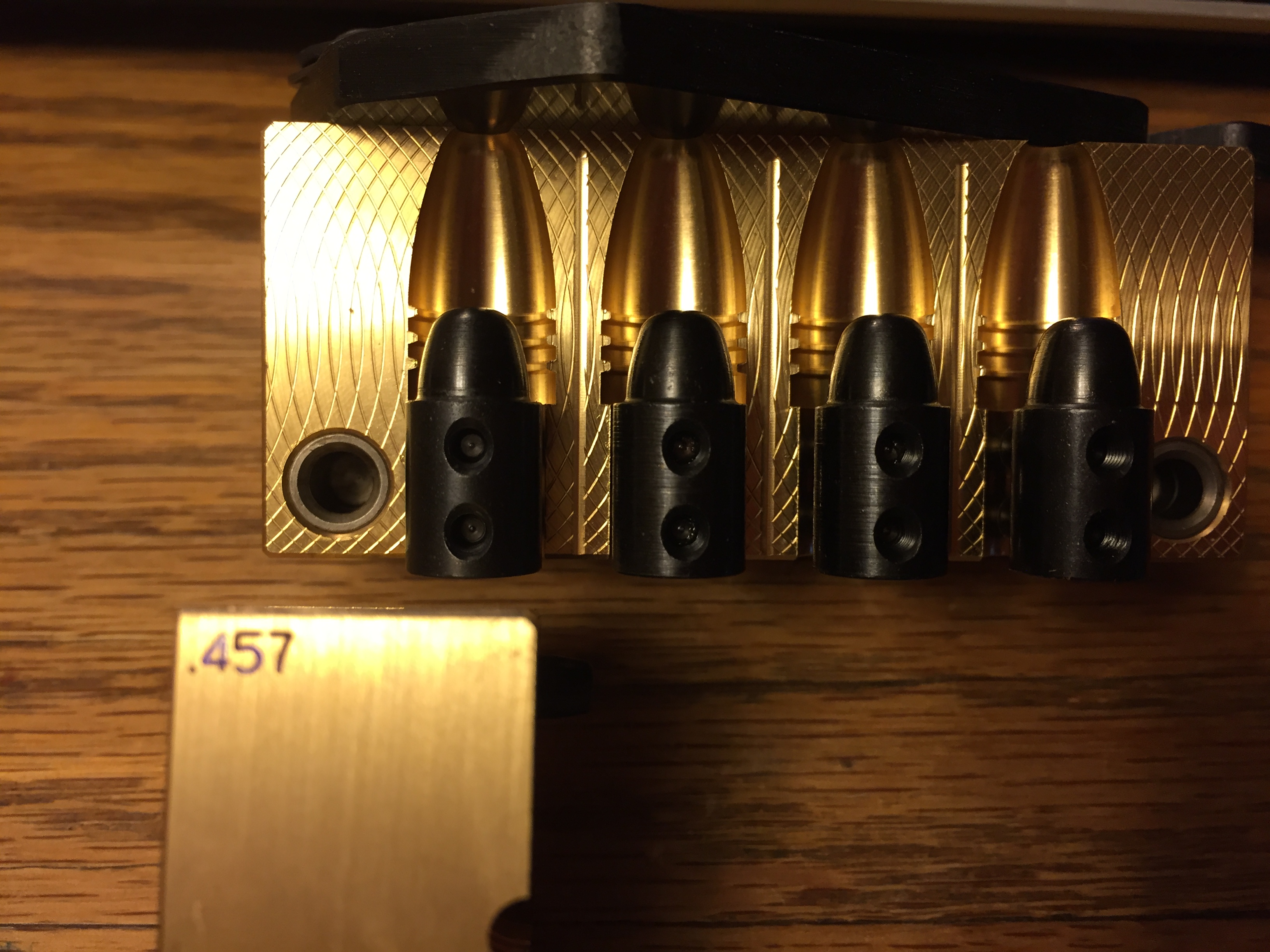
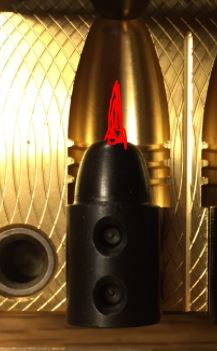
Any ideas? Tricks?