Cherokee
Medina, Ohio
OK, here are some pic's from this morning's attempt. Still have the little pocket but there appears to be an irregularity on the hinge side of the 6th cavity. Several pics:
#1 Cast that cavity only, note odd shape on hinge side near the parting line
#2 Can see the irregularity
#3 The offending depression
#4 Trying to show the irregularity on the hinge side
No petroleum solvent, soap & water with tooth brush for cleaning. Casting in heated indoors, about 69*, the same as summer with the AC going. Preheated on hot plate with the blocks closed.
That cavity is the last one poured, and it does look like it is not casting a good body like the other 5 cavities. Now that it's cooled down, I'm going to examine it again.
#1 Cast that cavity only, note odd shape on hinge side near the parting line
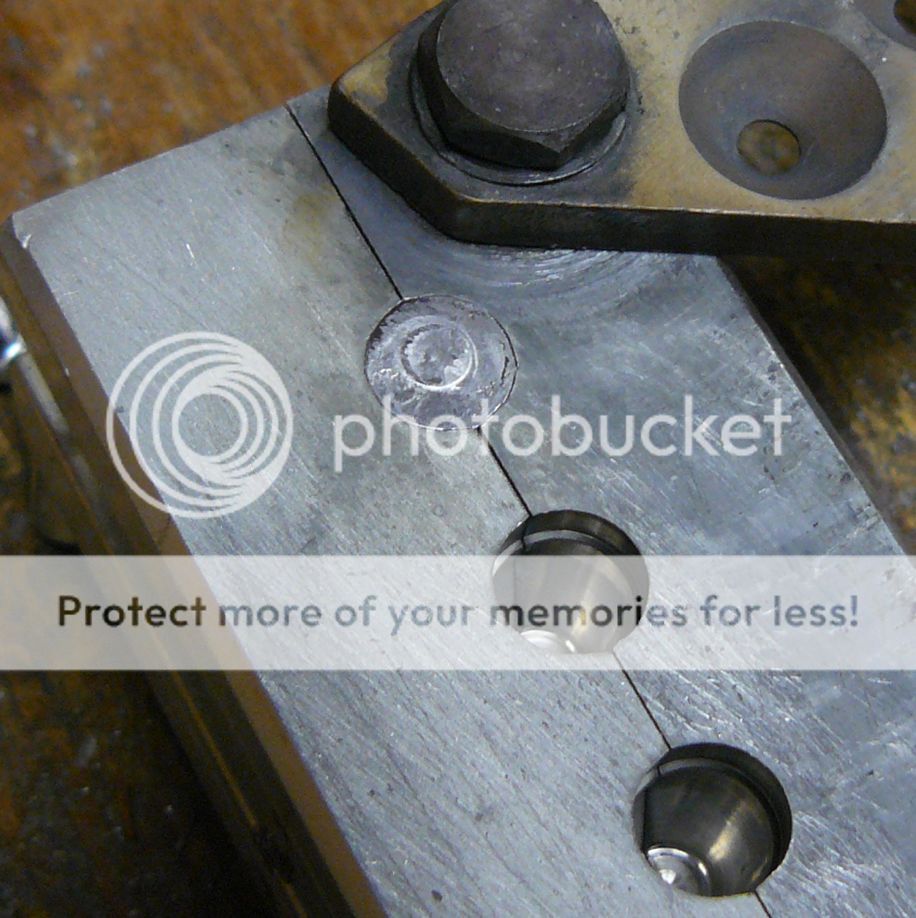
#2 Can see the irregularity
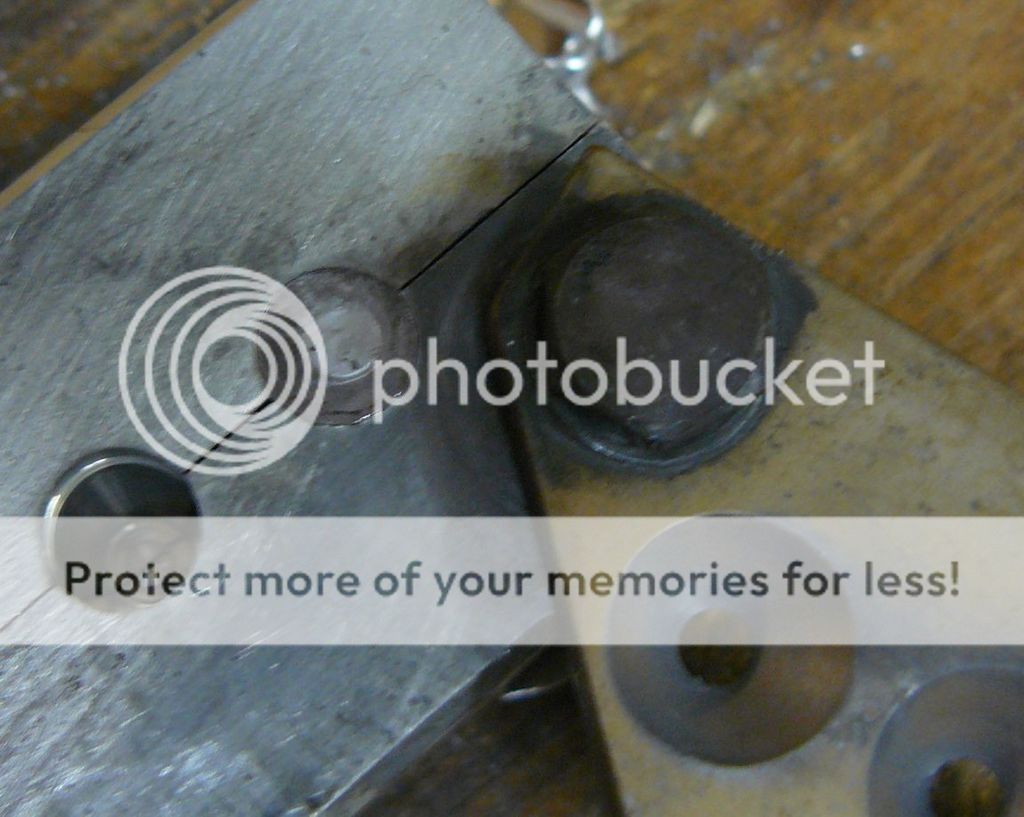
#3 The offending depression
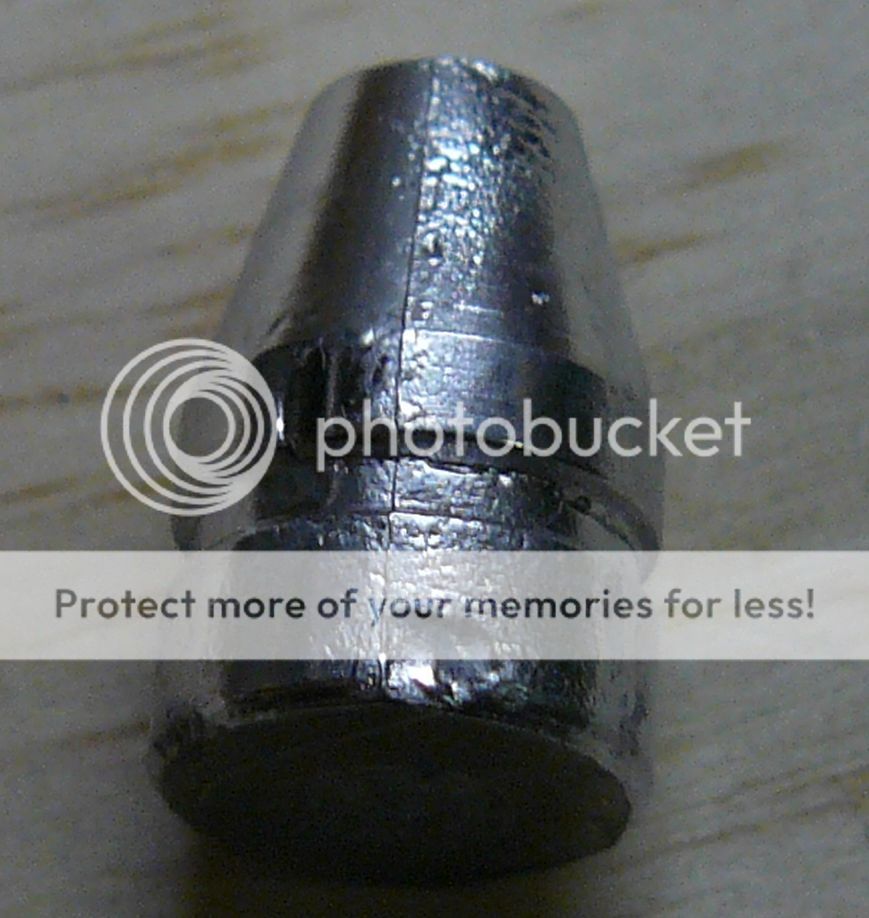
#4 Trying to show the irregularity on the hinge side
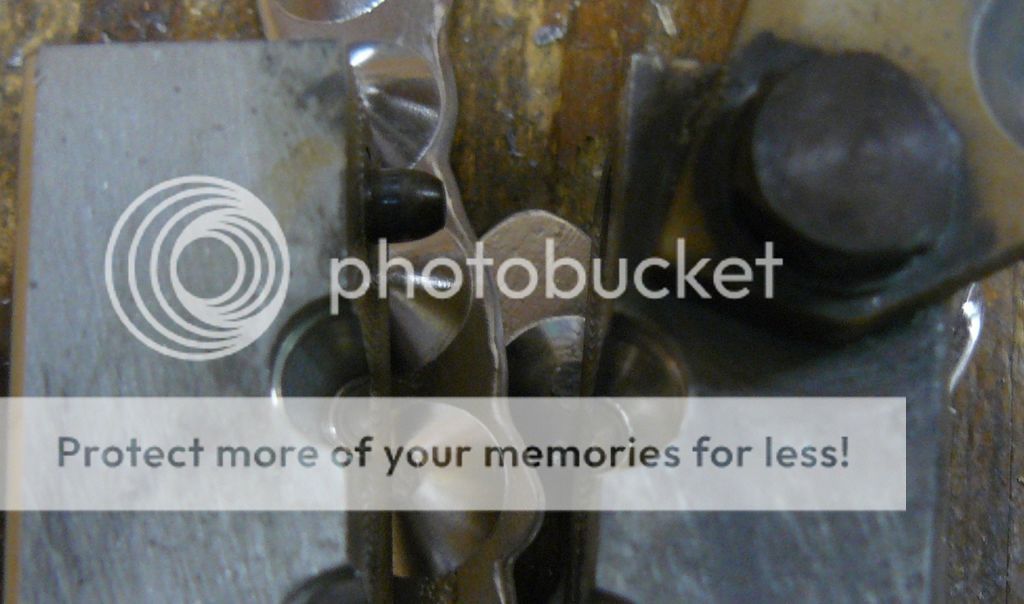
No petroleum solvent, soap & water with tooth brush for cleaning. Casting in heated indoors, about 69*, the same as summer with the AC going. Preheated on hot plate with the blocks closed.
That cavity is the last one poured, and it does look like it is not casting a good body like the other 5 cavities. Now that it's cooled down, I'm going to examine it again.