wquiles
Well-Known Member
My friend and mentor only uses HTP welding machines, and after he convinced me to get a local welding class, he also encouraged me to save my money and buy an HTP welder. I did, of course, and back in 2013 I bought a new HTP Mig 200 welder, which has been 100% flawless so far. So when I told him I wanted to learn and get a Tig setup, since he is no longer welding commercially/professionally, he offered to sell me his HTP Tig setup - the whole thing: HTP Invertig 200 with the water cooler, welder cart (modded to hold two tanks), 25ft ground, 25ft water cooled CK20-R torch, 25-ft CK torch mounted amp control (5-pin), 25-ft foot control (5-pin), inner touch cable cover and outer leather cable snap cover, and all of the rods and tungsten tips he found:
After changing the 220v plug to the one I use in my garage, I did a few simple beads, but decided to start doing some welding to practice for real, so I tried doing some small tacks. I ordered this kit to get me started:
I felt the touch a little heavy for my taste, and I was not yet comfortable with the torch amp control, so I removed it for now and I am using the foot switch until I get more proficient:
These are guts of the water cooled head:
Torch became lighter and easier to maneuver, even did some tacks right handed (I am a lefty):
Did some small tacks:
and a straight weld (both side):
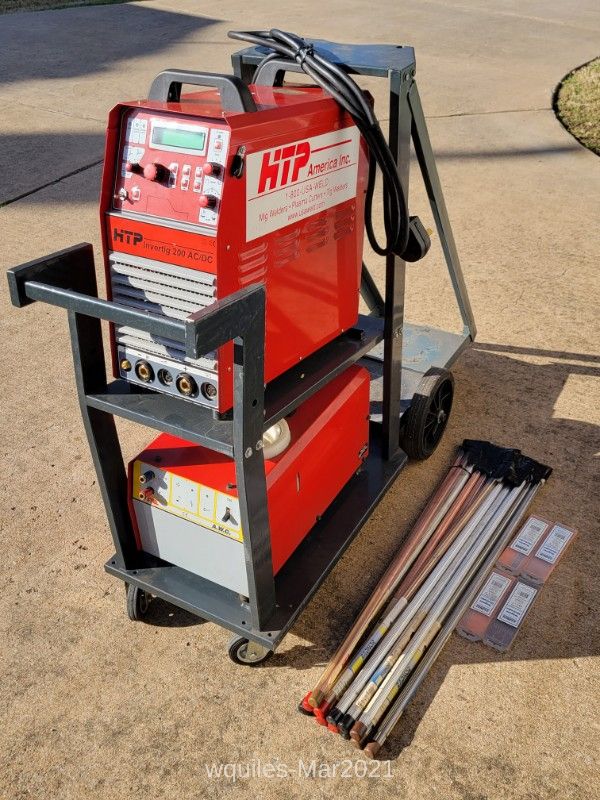
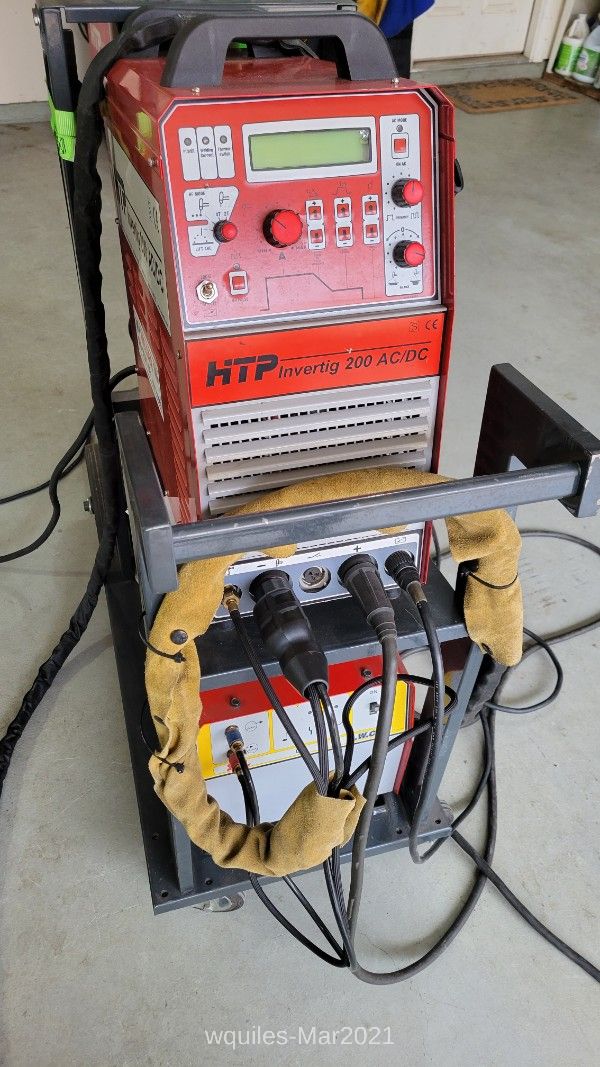
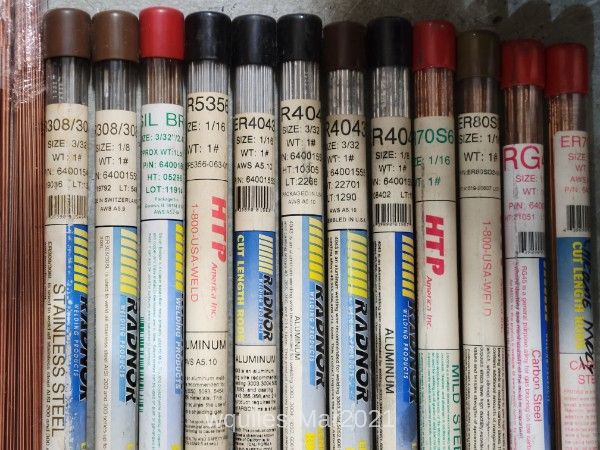
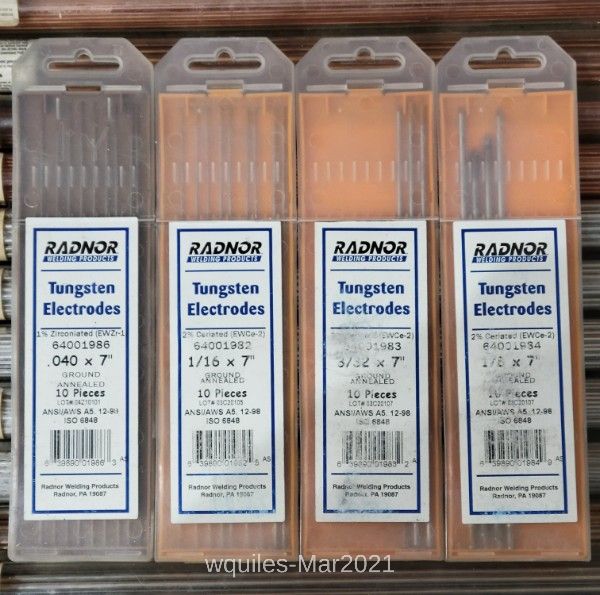
After changing the 220v plug to the one I use in my garage, I did a few simple beads, but decided to start doing some welding to practice for real, so I tried doing some small tacks. I ordered this kit to get me started:
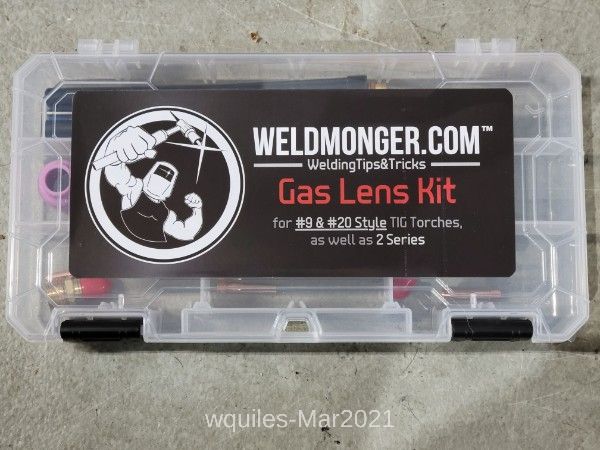
I felt the touch a little heavy for my taste, and I was not yet comfortable with the torch amp control, so I removed it for now and I am using the foot switch until I get more proficient:
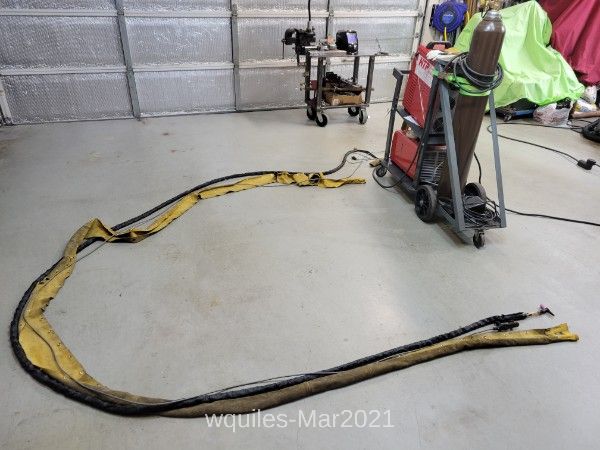
These are guts of the water cooled head:
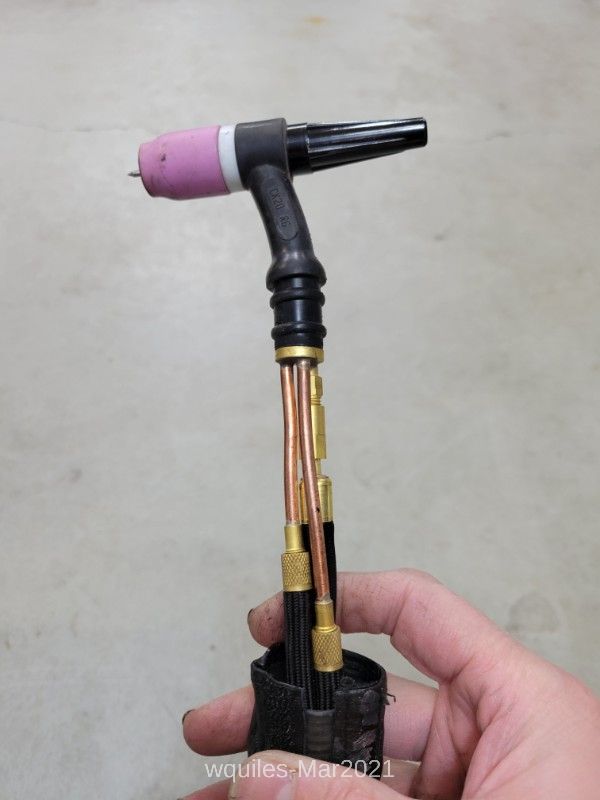
Torch became lighter and easier to maneuver, even did some tacks right handed (I am a lefty):
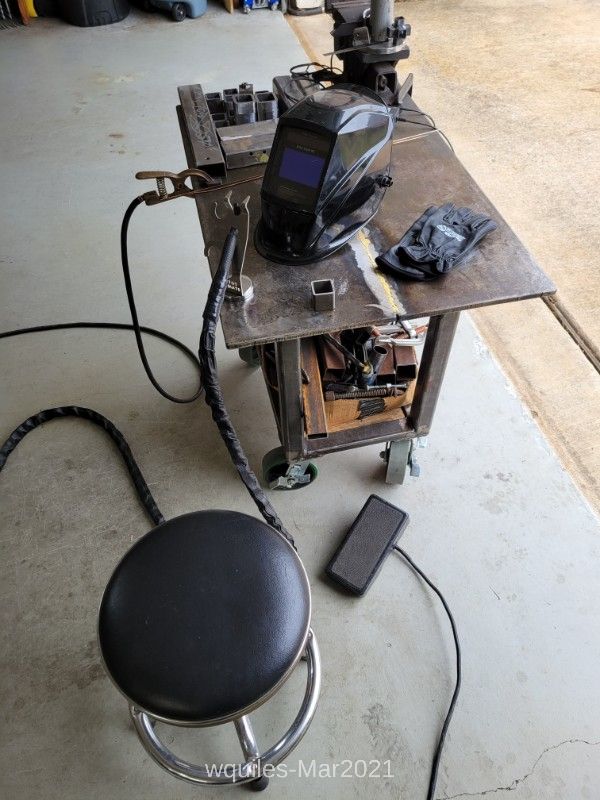
Did some small tacks:
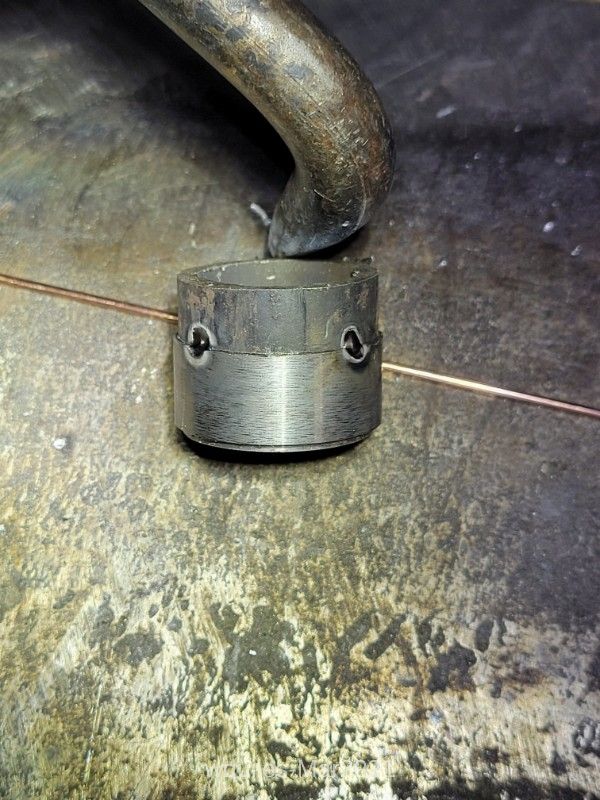
and a straight weld (both side):
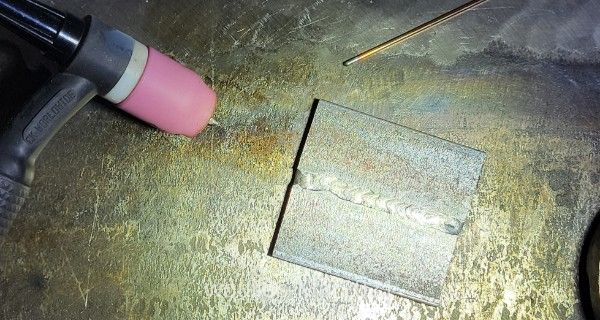