quicksylver
Well-Known Member
Hi guys..I think this question has been asked before..but here we go again..
I am not new to this so it has 'kinda taken me by surprise...
I had a bunch of old wheel weights given to me along with a bunch of other lead..
I thought I would smelt some the last couple of days since the weather has been a little damp..
The wheel weights I started with were some that look mostly unused , little to no smoke..nice..the first batch went pretty well..they melted fine , I fluxed a couple of thimes , took out the clips. they were nice and clean..
I poured them into ingot and started a second batch..
This batch I mixed a couple of lots that I had....they melted sort of ..but there was a lot of slurry mixed in..I fluxed a couple of times but it didn't seem to do much good.. I picked the clips out one at a time ..they were covered with a tin layer of alloy...I got them all out and refluxed..the slurry was still there..so I said to heck with it and skimmed the it off and poured what was left into ingots...
So before trying this again I thought it would be a brilliant idea to run it by you guys to see what you had to say..I am 'kinda thinking my temp may have been a little too low...but again first batch great second batch not worth mentioning...Dan
I am not new to this so it has 'kinda taken me by surprise...
I had a bunch of old wheel weights given to me along with a bunch of other lead..
I thought I would smelt some the last couple of days since the weather has been a little damp..
The wheel weights I started with were some that look mostly unused , little to no smoke..nice..the first batch went pretty well..they melted fine , I fluxed a couple of thimes , took out the clips. they were nice and clean..
I poured them into ingot and started a second batch..
This batch I mixed a couple of lots that I had....they melted sort of ..but there was a lot of slurry mixed in..I fluxed a couple of times but it didn't seem to do much good.. I picked the clips out one at a time ..they were covered with a tin layer of alloy...I got them all out and refluxed..the slurry was still there..so I said to heck with it and skimmed the it off and poured what was left into ingots...
So before trying this again I thought it would be a brilliant idea to run it by you guys to see what you had to say..I am 'kinda thinking my temp may have been a little too low...but again first batch great second batch not worth mentioning...Dan
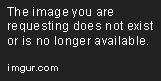
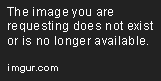
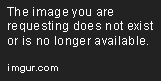
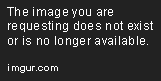