Mike W1
Active Member
Years back I made the little shelf for my Lee 10# to use to preheat my Lyman moulds and have always been satisfied with the results. By the time alloy is up to temperature so is the mould. First bullets out are always visually good if I pour em' right. Shelf temperature is in the 300° range which apparently is adequate for a Lyman mould.
That wasn't enough for a Lee that I purchased! The hot plate takes care of this one though. Also PID controlled, first bullets out are good. Little extension on the shelf was made adjustable so I could lay the mould flat on the shelf but I've removed it since determining I wasn't going to get the Lee hot enough.
Will continue using the shelf on the iron ones. Don't have any brass moulds so cannot say how the shelf would work on them.
That wasn't enough for a Lee that I purchased! The hot plate takes care of this one though. Also PID controlled, first bullets out are good. Little extension on the shelf was made adjustable so I could lay the mould flat on the shelf but I've removed it since determining I wasn't going to get the Lee hot enough.
Will continue using the shelf on the iron ones. Don't have any brass moulds so cannot say how the shelf would work on them.
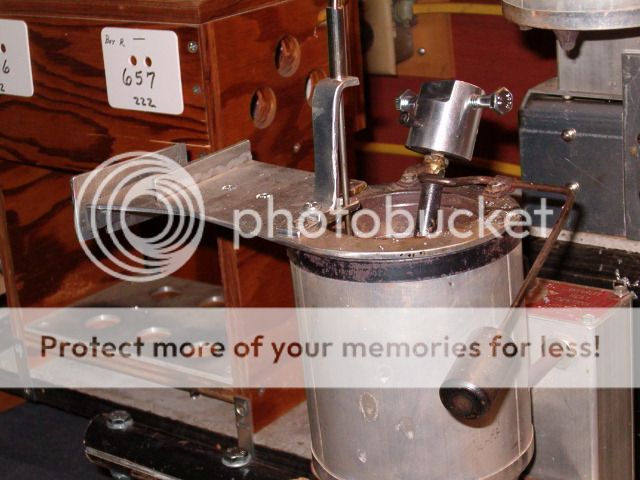