Snakeoil
Well-Known Member
I need things in the winter to maintain my sanity. I picked up a Browning 1885 Tradtional Hunter in .38-55 from a friend. We shoot out to 500 yds at one of the clubs I frequent and I was looking for reduced recoil from my .45-70 Shiloh Sharps.
The Browning is a nice rifle. Heavy enough for accurate shooting off a bench or sticks, and yet light enough to be used as an offhand piece. It comes with a Marble's tang sight that is pretty cheesy. I was able to get out to 300 yds with it last week, but ran out of sight after that.
I'm going to mount my Lyman Super Target Spot on the rifle and have been struggling to get Steve Earle to respond so I can order a set of mounting blocks from him. So, I decided to make a base so I can put my Soule long range tang sight on the High Wall.
It was a 3 day projects. Started out with a piece of 1/2 x 3/4 x 3" cold rolled steel. My mill is a tiny little Atlas horizontal mill. This was really a job for a Bridgeport, but alas, no Bridgeport in my shop. Probably spent as much time noodling onhow to set up the piece and the sequence of machining steps as I did actually machining the piece. Hit a few snags along the way, but was expecting that and came up with alternate ways to do what did not work on the first try.
Base came out pretty nice. Fits the rifle and the sight staff like it should. Made the detent spring from a piece of boxspring wire I had in the garage. Forged it to a flat spring with a bulb on the end to ride on the sight and engage the detent slot. My first try at the spring looked great. But my tempering was flawed and it broke after a couple of cycles. Not deterred, today, I forged a new spring from the same spring wire and used a different tempering technique that did the trick. This sight should get me out to 1000 yds if I take the rifle to Dry Lake in the summer.
Here's a few pics.
Here's the finished base before bluing.
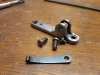
Had a minor set back with the first spring. Poor spring tempering on my part.
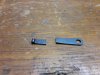
New spring made and the sight mounted on the rifle with the new base.
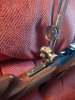
The Browning is a nice rifle. Heavy enough for accurate shooting off a bench or sticks, and yet light enough to be used as an offhand piece. It comes with a Marble's tang sight that is pretty cheesy. I was able to get out to 300 yds with it last week, but ran out of sight after that.
I'm going to mount my Lyman Super Target Spot on the rifle and have been struggling to get Steve Earle to respond so I can order a set of mounting blocks from him. So, I decided to make a base so I can put my Soule long range tang sight on the High Wall.
It was a 3 day projects. Started out with a piece of 1/2 x 3/4 x 3" cold rolled steel. My mill is a tiny little Atlas horizontal mill. This was really a job for a Bridgeport, but alas, no Bridgeport in my shop. Probably spent as much time noodling onhow to set up the piece and the sequence of machining steps as I did actually machining the piece. Hit a few snags along the way, but was expecting that and came up with alternate ways to do what did not work on the first try.
Base came out pretty nice. Fits the rifle and the sight staff like it should. Made the detent spring from a piece of boxspring wire I had in the garage. Forged it to a flat spring with a bulb on the end to ride on the sight and engage the detent slot. My first try at the spring looked great. But my tempering was flawed and it broke after a couple of cycles. Not deterred, today, I forged a new spring from the same spring wire and used a different tempering technique that did the trick. This sight should get me out to 1000 yds if I take the rifle to Dry Lake in the summer.
Here's a few pics.
Here's the finished base before bluing.
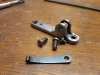
Had a minor set back with the first spring. Poor spring tempering on my part.
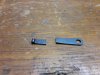
New spring made and the sight mounted on the rifle with the new base.
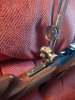