Necessity is the mother of invention, or so I was told as a child.
I like to load handgun cartridges on the Dillon 550. I also like to seat and crimp in separate steps. That eliminates the ability to seat bullets, readjust the die, then crimp.
I have a nice Redding Profile crimp die but it won't work with the .433 bullets I am currently feeding the Marlin 1894. I decided that since I had already modified the Hornady seater and figure out the crimp step I would make an entire new crimp die.
I made it from 12L14 as it won't see much real wear. That steel also machines so nice that it makes everything easy.
The interior was drilled to .422. I then used a small boring bar to cut the bottom section to .434 so the bullets would easily fit. The crimp step was located and I bored the bottom section to .457 so a loaded round fit easily. I cut a slight taper on the lower 1/2 inch then beveled the opening to ensure a flared case mouth would enter.
Works just like I wanted it should.
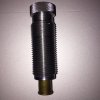
I like to load handgun cartridges on the Dillon 550. I also like to seat and crimp in separate steps. That eliminates the ability to seat bullets, readjust the die, then crimp.
I have a nice Redding Profile crimp die but it won't work with the .433 bullets I am currently feeding the Marlin 1894. I decided that since I had already modified the Hornady seater and figure out the crimp step I would make an entire new crimp die.
I made it from 12L14 as it won't see much real wear. That steel also machines so nice that it makes everything easy.
The interior was drilled to .422. I then used a small boring bar to cut the bottom section to .434 so the bullets would easily fit. The crimp step was located and I bored the bottom section to .457 so a loaded round fit easily. I cut a slight taper on the lower 1/2 inch then beveled the opening to ensure a flared case mouth would enter.
Works just like I wanted it should.
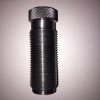
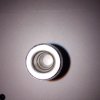
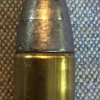
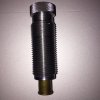