Brother_Love
Well-Known Member
I finally got some casting done today since it was a little cooler (94). The 35's are from a new NOE mold that I prepared just as the instructions directed me. You can see from the photos that some of the bullets look almost perfect and others look really bad. I had to cast a little hotter than I like to get the mold to fill out right.
I am not going to get my feelings hurt, I really want to know what I am doing wrong. My pot was just cleaned out 2 weeks ago and I am using Lyman #2.
The .30 caliber was cast from a Lyman mold for a 30-06. I use Aluminum molds but I prefer a steel mold and I seem to cast better with them.
Thank you, Malcolm
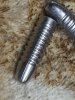
I am not going to get my feelings hurt, I really want to know what I am doing wrong. My pot was just cleaned out 2 weeks ago and I am using Lyman #2.
The .30 caliber was cast from a Lyman mold for a 30-06. I use Aluminum molds but I prefer a steel mold and I seem to cast better with them.
Thank you, Malcolm
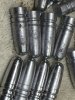
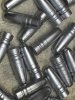
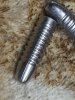