I have someone who is getting into paper patching. He wanted a way to size bullets down before rolling them.
I made a .307, .302, and .301 sizer along with a pusher that is a snug fit in the .301 sizer.
I found a faster way to complete these. I discovered that running the lathe at a higher RPM let me get a better finish and take a heavier cut. I also finish the outside dimensions, cut the part off, then drill. I don't cut the threads until the last step. I have it down to about an hour per die. Much of that is the final trial and error polishing.
I made a .307, .302, and .301 sizer along with a pusher that is a snug fit in the .301 sizer.
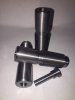
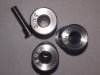
I found a faster way to complete these. I discovered that running the lathe at a higher RPM let me get a better finish and take a heavier cut. I also finish the outside dimensions, cut the part off, then drill. I don't cut the threads until the last step. I have it down to about an hour per die. Much of that is the final trial and error polishing.