I have told this story before. In a fit of frustration, after battling the weird tapered shank that came on the Lee 324-175 mold. I drilled out the shank, with a not so sharp drill bit. You can see in the photo that the finish isn’t that great. However I size these down to .318”. Most of the roughness on the bullet is removed during sizing.
I mentioned this the other day, in the sizing thread, that because the push rod is so tight in the Lee sizing die I don’t get any fins on the base of this bullet.
And yes the base is slightly larger then the rest of the drive bands. It’s almost like what Doctor Frankenstein would do if he modified a mold.
Also, it engraves pretty deeply into the rifling.
That mold sure has taught me a lot about what you can do, right and wrong!
Josh
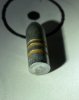