G/C Seating Tool
Ben's Gas Check Seating Die
For about as long as I can remember ( & I starting reloading in 1965 ), I've had problems seating a g/c on the shank of a bullet squarely. This problem is aggravated by g/c shanks that are a few thousandths of an inch too large.
I've tried about every method and had only partial success. I realized early that the real problem that continued to be the culprit of my g/c seating problems was the ability to achieve perfect coaxial alignment with the center line of the bullet and the gas check that the shank was about to enter.
The different methods that I'd been using just did not have the precision necessary to accomplish the task. Time for a new design and a man that could make it. I contacted Buckshot about my idea that I had for seating gas checks. I asked him if he could make the die to my specs ? His reply was " YES ".
I took a lot of measurements of a .30 cal. Hornady g/c, width, height, etc. and drew a sketch of the exact dimensions that would be necessary for the tool to work properly and sent those drawings to Buckshot. Now it would be a matter of time to pass until the idea would turn into a functioning tool.
My idea was to make a die ( hand operated tool on your bench - - there was to be no reloading press needed ) that is .3120" in it's inside bore. The underside of the die has a recess cut ( tight tolerances....no wiggle room ) for a Hornady .30 cal. gas check.
The die was to be .630 " in height, I felt that was plenty tall enough to accommodate all of the bearing surface ( drive bands ) on any of my .30 cal. cast bullets and keep the main body of the bullet in perfect coaxial alignment with the center line of the bullet and the gas check .
In order for the die to work properly, you'll need ANY .30 cal. cast bullet with any nose style that is 1st sized to a perfect .3110" in diameter. I simply push a .30 cal. cast bullet ( lightly lubed ) through a Lee Bullet sizing die that I have honed to size a bullet EXACTLY .3110 in diameter. This keeps the die and the bullet in tight tolerances with each other and guarantees perfect alignment and seating of the g/c properly.
At this point in time, it is obvious that the die is caliber specific causing one to need a 2nd die cut to very critical tolerances to use it with another caliber.
When I size one of my .30 cal. cast bullets in a Lee Bullet sizing die that I have honed to EXACTLY .3110 " dia., that bullet can be slid with some thumb pressure down the bore of the die.
When a g/c is in place and the .311 cast bullet placed in the bore of the die, all that is left to do is to place your top punch that fits your cast bullet on the nose of the bullet and give a couple of soft taps with a small tack hammer. The g/c is seated perfectly every time. The g/c isn't crimped at this point in time. All you have to do now is pass the g/c'd bullet back through a .311 sizer die , or .310 or .309"...( your choice ) in order to crimp and lock the g/c onto the shank of the bullet.
The beauty of the system is no crooked and cock - eyed looking gas checks anymore. The bullet goes into the gas check with no possibility of mis-alignment ( which had always been the Achilles' Heel of all my other attempts in the past ). In the past, if the bullet entered the g/c just a few degrees out of alignment, you'd always end up with the g/c on the base of the bullet , in a mis-aligned fashion. We all know what this does to accuracy. No more mis-aligned checks now !
Once the g/c is seated onto the g/c shank of the bullet, soft thumb pressure will eject the bullet from the die and you're ready for the next one. It is a quick system and a SUPER ACCURATE system with no mis-alignment.
I know.....You want one, Right ? ?
Well, you'll need to contact Buckshot, the tool was made with my plans and by my specs that I wrote up and provided Buckshot.
I have no interest in making a single penny from any aspect of this endeavor.
If you want one, you need to contact Buckshot .
BTW, I know of no reason why this concept can't be adapted to other calibers, .22, 6mm, .25, .264, 7mm, .35, .44, 45, etc.
I've been waiting for something like this for a LONG TIME !
Here is the " End Product " :
It really makes a difference down range..............
I sized my cast bullets in the group that you see below with my .3095" Lee Push thru sizing die after the gas checks were installed with my gas check seating tool.
Ben's Gas Check Seating Die
For about as long as I can remember ( & I starting reloading in 1965 ), I've had problems seating a g/c on the shank of a bullet squarely. This problem is aggravated by g/c shanks that are a few thousandths of an inch too large.
I've tried about every method and had only partial success. I realized early that the real problem that continued to be the culprit of my g/c seating problems was the ability to achieve perfect coaxial alignment with the center line of the bullet and the gas check that the shank was about to enter.
The different methods that I'd been using just did not have the precision necessary to accomplish the task. Time for a new design and a man that could make it. I contacted Buckshot about my idea that I had for seating gas checks. I asked him if he could make the die to my specs ? His reply was " YES ".
I took a lot of measurements of a .30 cal. Hornady g/c, width, height, etc. and drew a sketch of the exact dimensions that would be necessary for the tool to work properly and sent those drawings to Buckshot. Now it would be a matter of time to pass until the idea would turn into a functioning tool.
My idea was to make a die ( hand operated tool on your bench - - there was to be no reloading press needed ) that is .3120" in it's inside bore. The underside of the die has a recess cut ( tight tolerances....no wiggle room ) for a Hornady .30 cal. gas check.
The die was to be .630 " in height, I felt that was plenty tall enough to accommodate all of the bearing surface ( drive bands ) on any of my .30 cal. cast bullets and keep the main body of the bullet in perfect coaxial alignment with the center line of the bullet and the gas check .
In order for the die to work properly, you'll need ANY .30 cal. cast bullet with any nose style that is 1st sized to a perfect .3110" in diameter. I simply push a .30 cal. cast bullet ( lightly lubed ) through a Lee Bullet sizing die that I have honed to size a bullet EXACTLY .3110 in diameter. This keeps the die and the bullet in tight tolerances with each other and guarantees perfect alignment and seating of the g/c properly.
At this point in time, it is obvious that the die is caliber specific causing one to need a 2nd die cut to very critical tolerances to use it with another caliber.
When I size one of my .30 cal. cast bullets in a Lee Bullet sizing die that I have honed to EXACTLY .3110 " dia., that bullet can be slid with some thumb pressure down the bore of the die.
When a g/c is in place and the .311 cast bullet placed in the bore of the die, all that is left to do is to place your top punch that fits your cast bullet on the nose of the bullet and give a couple of soft taps with a small tack hammer. The g/c is seated perfectly every time. The g/c isn't crimped at this point in time. All you have to do now is pass the g/c'd bullet back through a .311 sizer die , or .310 or .309"...( your choice ) in order to crimp and lock the g/c onto the shank of the bullet.
The beauty of the system is no crooked and cock - eyed looking gas checks anymore. The bullet goes into the gas check with no possibility of mis-alignment ( which had always been the Achilles' Heel of all my other attempts in the past ). In the past, if the bullet entered the g/c just a few degrees out of alignment, you'd always end up with the g/c on the base of the bullet , in a mis-aligned fashion. We all know what this does to accuracy. No more mis-aligned checks now !
Once the g/c is seated onto the g/c shank of the bullet, soft thumb pressure will eject the bullet from the die and you're ready for the next one. It is a quick system and a SUPER ACCURATE system with no mis-alignment.
I know.....You want one, Right ? ?
Well, you'll need to contact Buckshot, the tool was made with my plans and by my specs that I wrote up and provided Buckshot.
I have no interest in making a single penny from any aspect of this endeavor.
If you want one, you need to contact Buckshot .
BTW, I know of no reason why this concept can't be adapted to other calibers, .22, 6mm, .25, .264, 7mm, .35, .44, 45, etc.
I've been waiting for something like this for a LONG TIME !
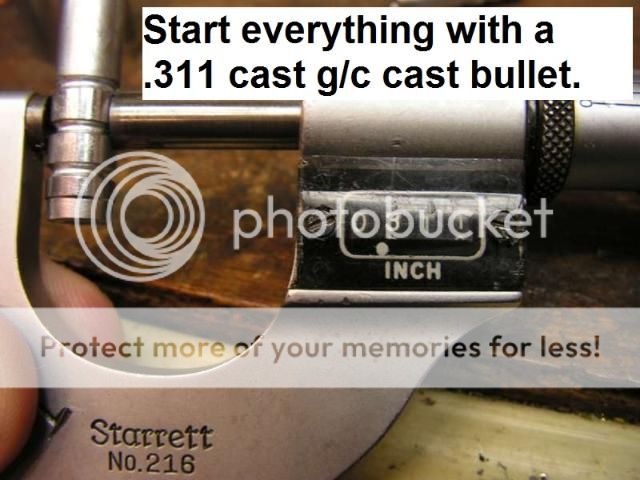
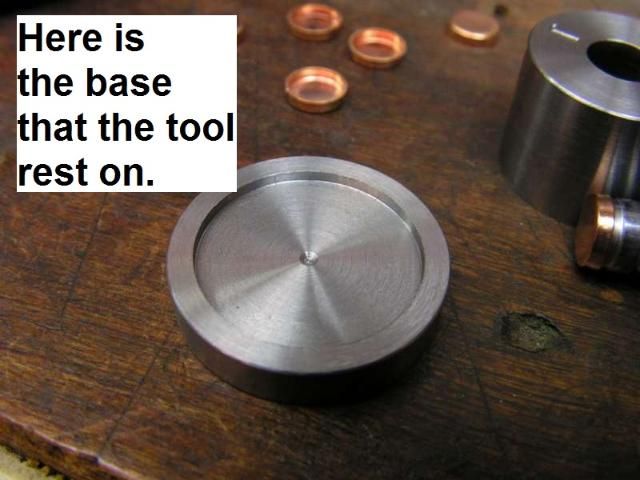
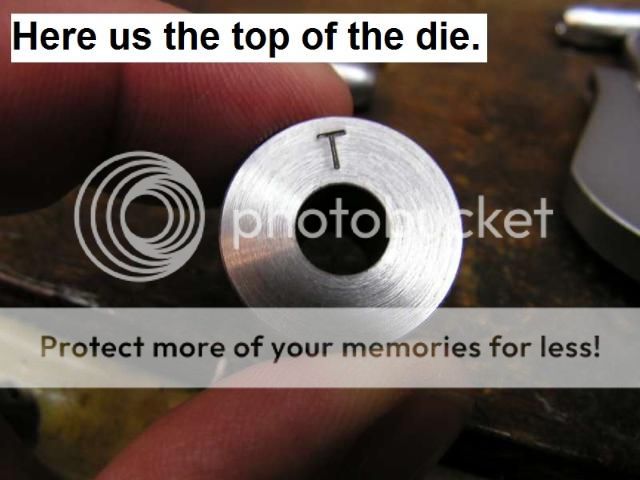
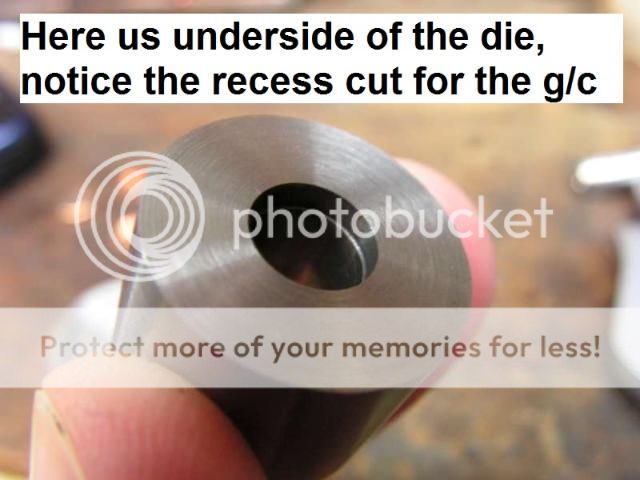
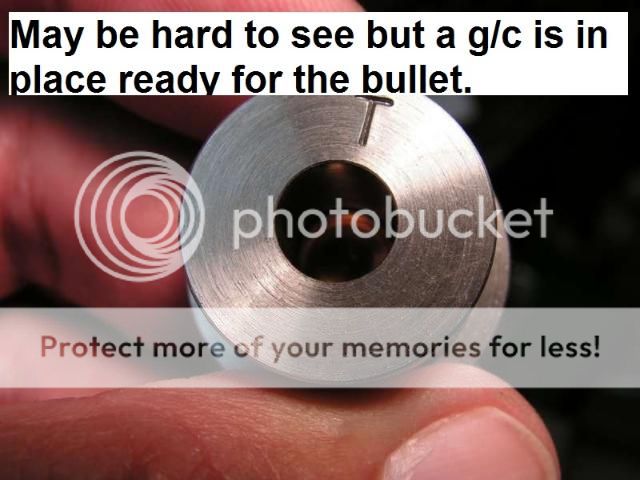
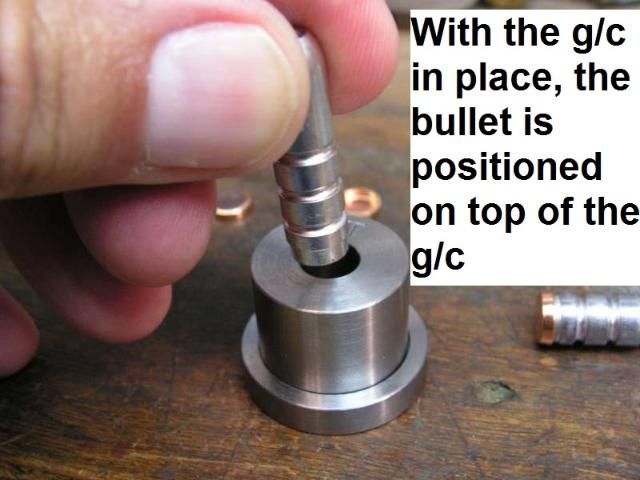
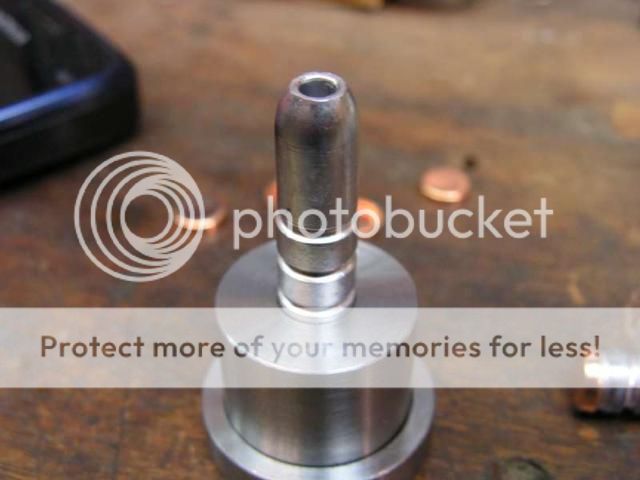
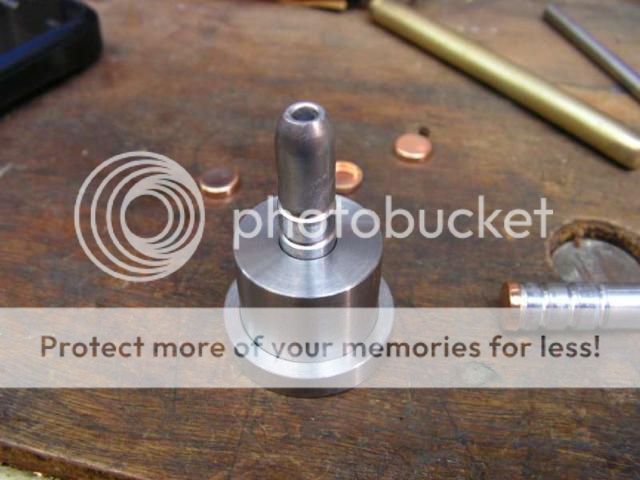
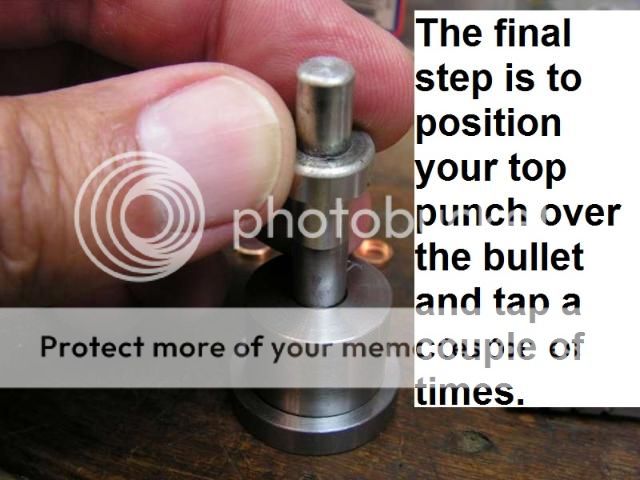
Here is the " End Product " :
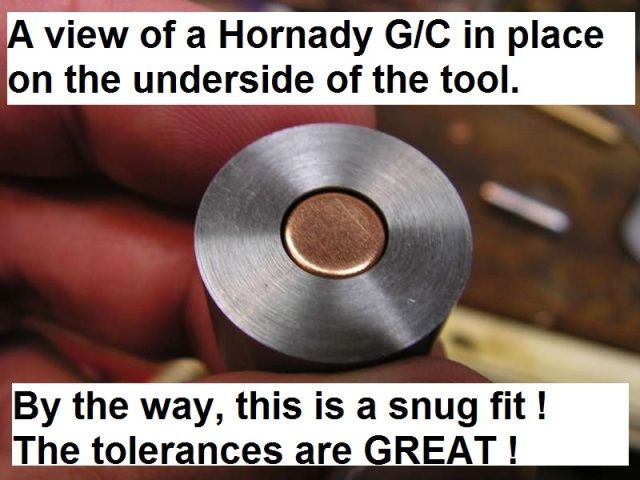
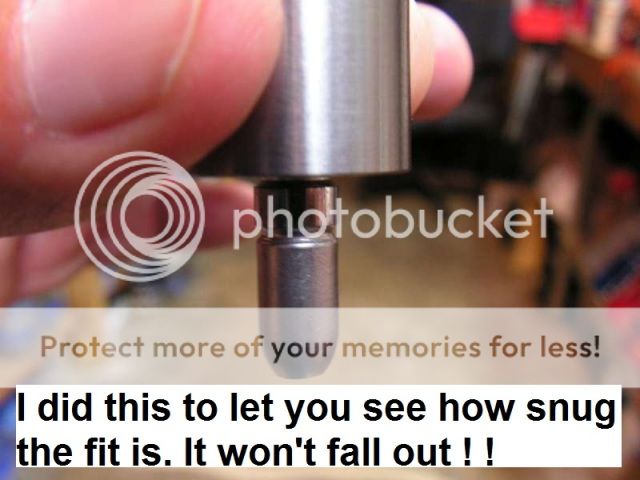
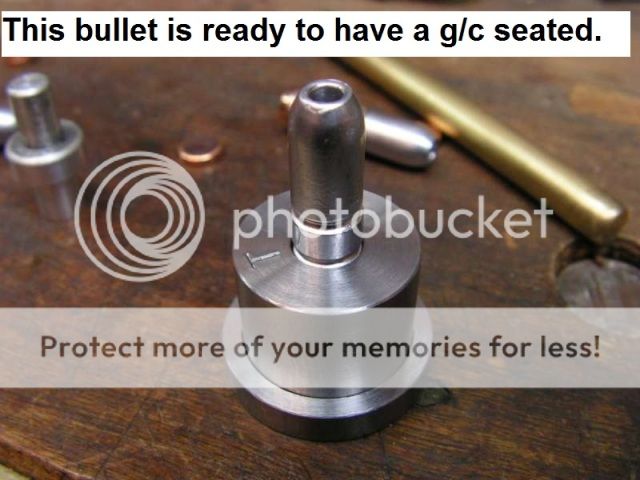
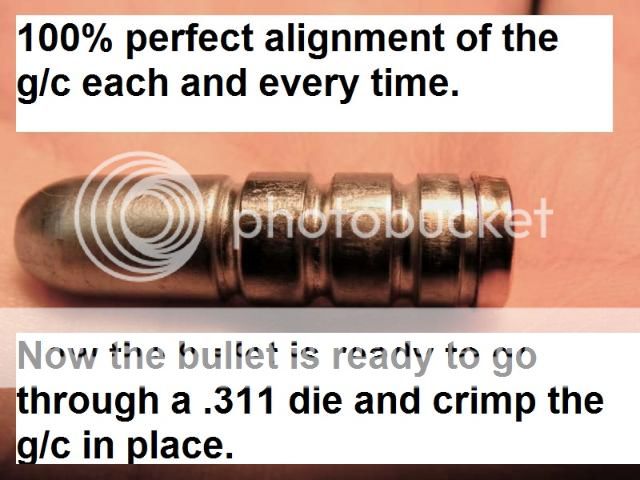
It really makes a difference down range..............
I sized my cast bullets in the group that you see below with my .3095" Lee Push thru sizing die after the gas checks were installed with my gas check seating tool.
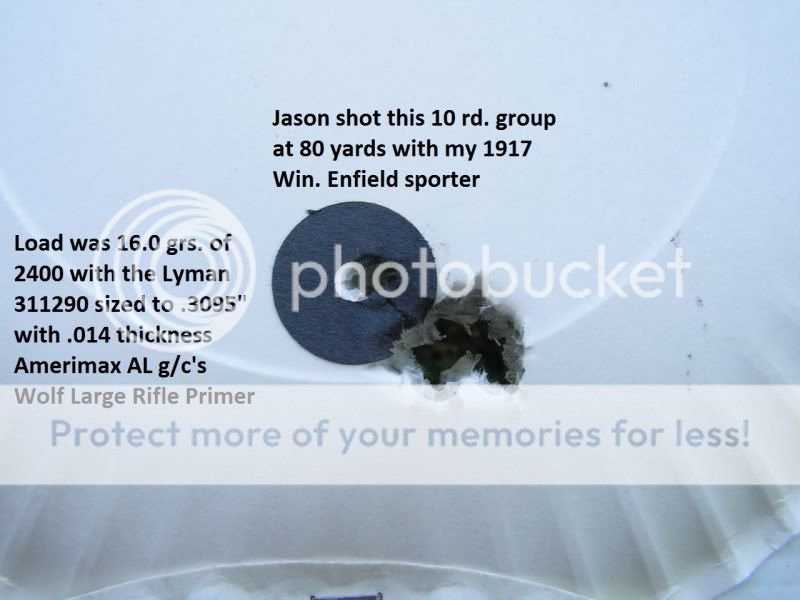
Last edited: