Ok Ben, I had to make this better. The hammer was driving me nuts. (Pun intended)
Why not make the tool so the bullet will always be the same length after searing the check to ensure they are seated the same?
I decided to use my loading press instead of a hammer. This is the check searing die like you have and my base. Notice my base is made to use the shell holder slot in the press?
Bullet with a check in die. The die is cut to the exact same length as a checked bullet. No way to deform the bullet excessively as the die prevents the bullet from becoming shorter than a sized and checked bullet. Makes it pretty fool proof.
Base in press, bullet in die, die on base.
Check being seated. Ram is raised very little. At this point in stroke the press develops little force compared to at full strength. Plenty of force to seat the check.
Base, anvil die from flair tool, and check seating die. Notice the base unit is bored to fit the seating die.
Bullet with seated check. This bullet requires a flaired check to ensure seating is full and square. This tool does the same job.
The downside is that a separate seating die is required for each diameter and bullet design. Bore in seating die was bored to fit the diameter I use for this bullet in my 300 BO. The bullet determines the required length of the seating die.
Sure was good to run the lathe again. Been 4 long weeks. Everything went well, it all came together nicely. Can't think of a better way to spend an hour or two.
Why not make the tool so the bullet will always be the same length after searing the check to ensure they are seated the same?
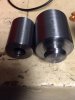
I decided to use my loading press instead of a hammer. This is the check searing die like you have and my base. Notice my base is made to use the shell holder slot in the press?
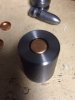
Bullet with a check in die. The die is cut to the exact same length as a checked bullet. No way to deform the bullet excessively as the die prevents the bullet from becoming shorter than a sized and checked bullet. Makes it pretty fool proof.
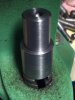
Base in press, bullet in die, die on base.
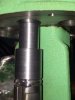
Check being seated. Ram is raised very little. At this point in stroke the press develops little force compared to at full strength. Plenty of force to seat the check.
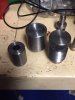
Base, anvil die from flair tool, and check seating die. Notice the base unit is bored to fit the seating die.
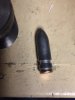
Bullet with seated check. This bullet requires a flaired check to ensure seating is full and square. This tool does the same job.
The downside is that a separate seating die is required for each diameter and bullet design. Bore in seating die was bored to fit the diameter I use for this bullet in my 300 BO. The bullet determines the required length of the seating die.
Sure was good to run the lathe again. Been 4 long weeks. Everything went well, it all came together nicely. Can't think of a better way to spend an hour or two.