Do you ever have trouble getting gas checks to seat themselves squarely on the base of the bullet ? For me, a high % of the time, this is caused by either a gas check that is too small or a gas check shank on a bullet that is too large, or a bit of both.
This little .17 cent home - made tool can be a real game changer.
I have one for 7 mm, .30 cal., 8 mm, and .35 cal.
I wouldn't be without them.
I make mine from a 5" long steel bolt that is a " tad " larger than the inside of the gas check I want to flare. I cut the threads off with a hack saw. Square the end with a flat file. Then cut a slight taper on the end of the bolt ( see photo below ). A little bit of trial and error will get you a tool that will work perfectly each and every time.
Here is a pic of my .30 cal. gas check flare tool.
It makes all the difference in the world in your ability too seat a gas check squarely onto the shank of your bullet with your lube sizer.
Will the tool allow you to make accurate ammo ? You bet. My Savage .308 Win., 5 rounds at 50 yards yesterday :
Ben
This little .17 cent home - made tool can be a real game changer.
I have one for 7 mm, .30 cal., 8 mm, and .35 cal.
I wouldn't be without them.
I make mine from a 5" long steel bolt that is a " tad " larger than the inside of the gas check I want to flare. I cut the threads off with a hack saw. Square the end with a flat file. Then cut a slight taper on the end of the bolt ( see photo below ). A little bit of trial and error will get you a tool that will work perfectly each and every time.
Here is a pic of my .30 cal. gas check flare tool.
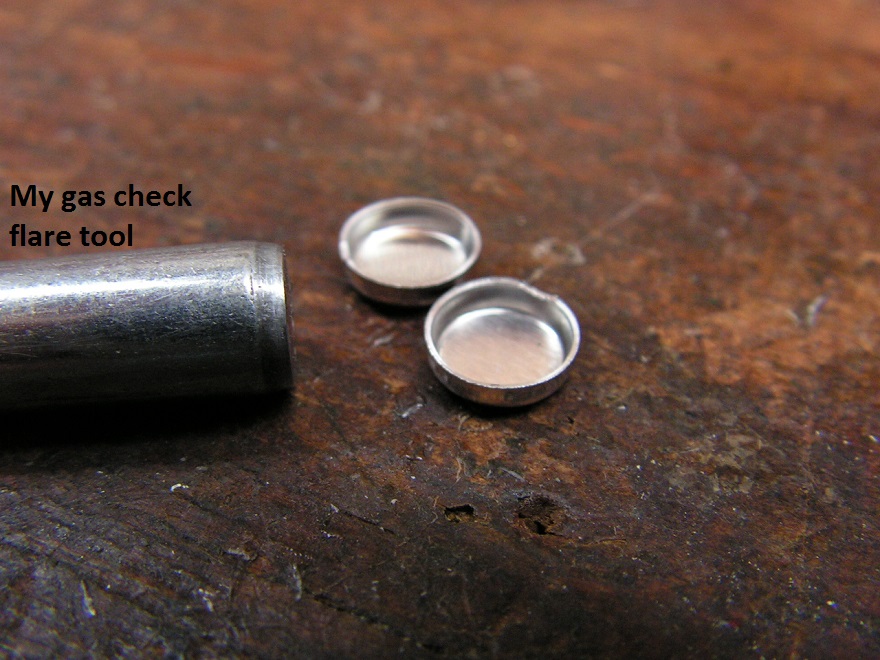
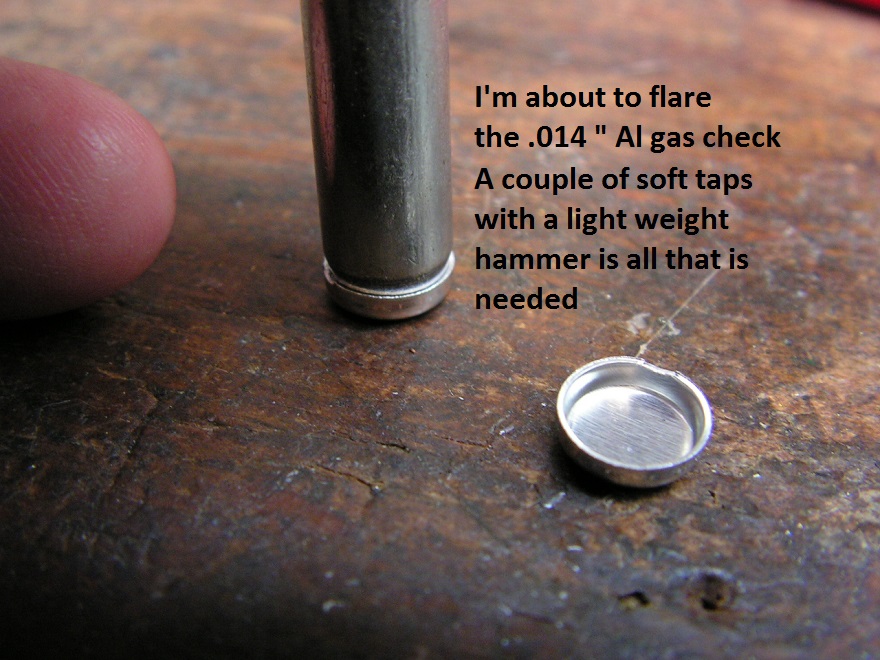
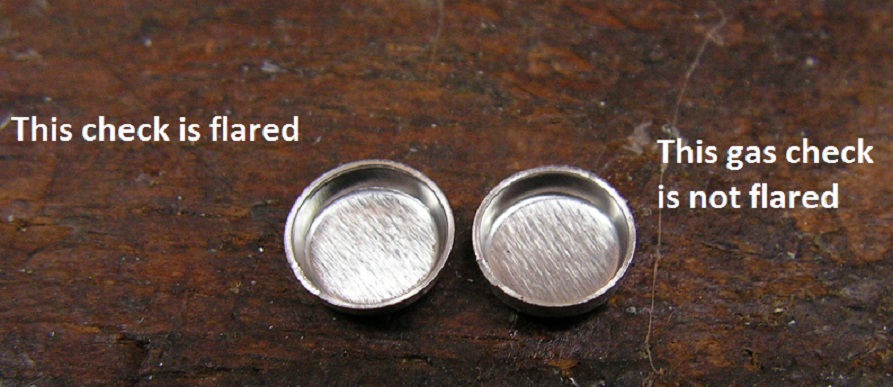
It makes all the difference in the world in your ability too seat a gas check squarely onto the shank of your bullet with your lube sizer.
Will the tool allow you to make accurate ammo ? You bet. My Savage .308 Win., 5 rounds at 50 yards yesterday :
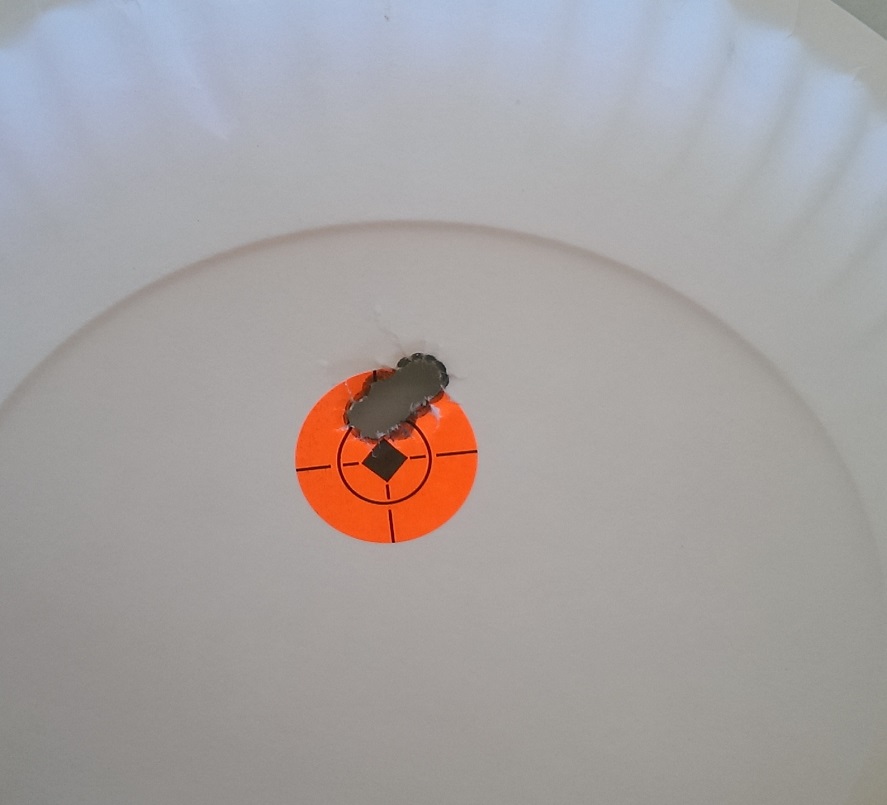
Ben
Last edited: